Interview
"I don't see a future where this doesn't exist”: Intramotev CEO on autonomous rail freight
Peter Nilson speaks with Timothy Luchini, CEO of Intramotev, about the company’s autonomous electric rail freight solution and future applications for the technology.
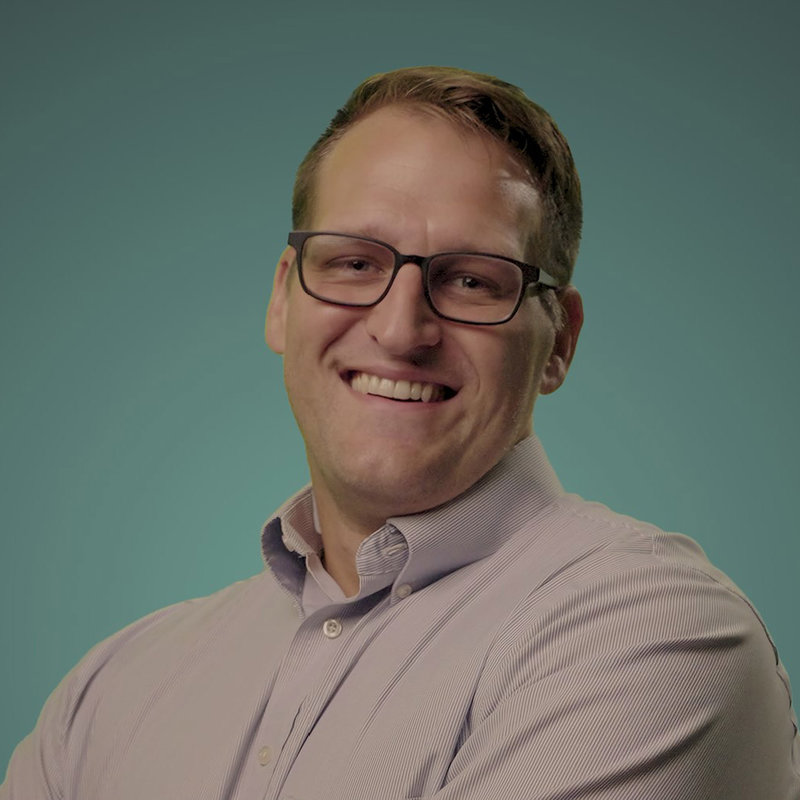
Timothy Luchini, Intramotev CEO.
US-based startup Intramotev is on a mission to take rail freight into a new era. The Missouri-based company is focusing on developing a battery electric autonomous rail car, enabling freight to move with the flexibility of a truck with the efficiency of rail.
Founded in 2020, the company draws on co-founder and CEO Timothy Luchini’s experience as an engineer at Boeing, working on urban air mobility and cargo air drones, moving packetised air freight using electric propulsion systems.
“Alex [Peiffer, Intramotev co-founder and COO] sent me a paper about battery electric hybrid locomotives, and he was asking me what I think about that tech in the context of rail,” Luchini recounts.
"I told him the truth. I think that it's an interesting incremental improvement on the current model, but maybe not transformational. And he said: ‘Okay, well what happens if you take all this tech that you're building for these cargo air drones – the autonomy systems, electric power systems, the motors, the batteries, the sensors – and then we applied that to rail?’”
The answer to this question, as Luchini explains, was the starting point for Intramotev.
"We started talking through the interesting elements of electrifying in that way and the challenges of automating the whole train, as far as the North American rail freight system goes,” he says.
The pair concluded that they could build something that could complement the current model of rail, which as Luchini admits “in many ways does a lot of things right” in terms of price and reliability; but is still beaten by road freight in terms of speed.
"If people want things inexpensively and in an environmentally friendly way, they go by rail,” he explains. “If they want things fast, then they go by trucking, which is five to ten times more expensive.”
Future Rail sat down with Luchini to find out more about the tech behind Intramotev’s new solutions, the obstacles that autonomous rail operations face, the company’s ambitions for the future, and how they believe they can take on traditional road freight.
Peter Nilson: Can you explain the new tech that Intramotev is developing?
Timothy Luchini: We have two primary products. One's called the TugVolt and one's called the ReVolt. The TugVolt is a rail car first and foremost, it has the standard North American air brake system and the standard North American coupling system and is compliant with North American safety standards. But we have modified that to allow for each rail car to drive itself. So, it can be backwards compatible and pulled in a train, but it can also enable point-to-point movement.
The way that we do that, is we take electric motor and we drive the axles on the car. Then we feed those electric motors through a series of motor controllers, inverters, and the battery backup that drives the power system for it. We have an onboard vehicle management system – a gateway to connect it to the networks – computer vision systems, and a series of computers running onboard to do all the processing of information that's taking place. It can be run in a remote or fully autonomous manner, depending on the use case and the flexibility required.
We designed it in three modes of operation: to be pulled in a normal train, as point-to-point independent motion, and pulling five fully loaded cars with it. With about 100 tonnes of payload onboard, you can get [a range] of 100 miles with 100 kilowatt hours of battery, which is about the size of a Tesla car.
Peter Nilson: And how does ReVolt work?
Timothy Luchini: The second product is called the ReVolt. And that is a TugVolt, but it's just designed to be used in a standard train. If you have a standard diesel engine at the front, and you mix in the ReVolts, you've hybridised the train.
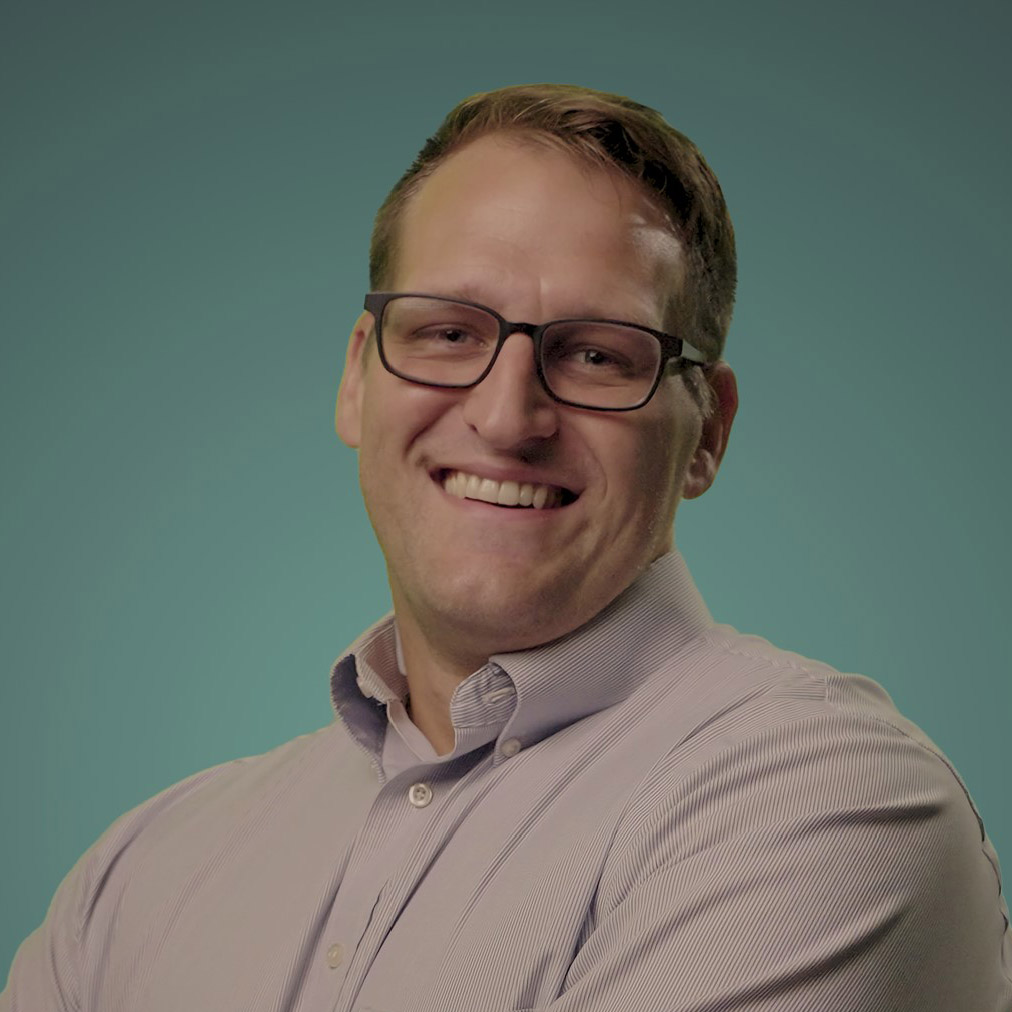
Caption. Credit:
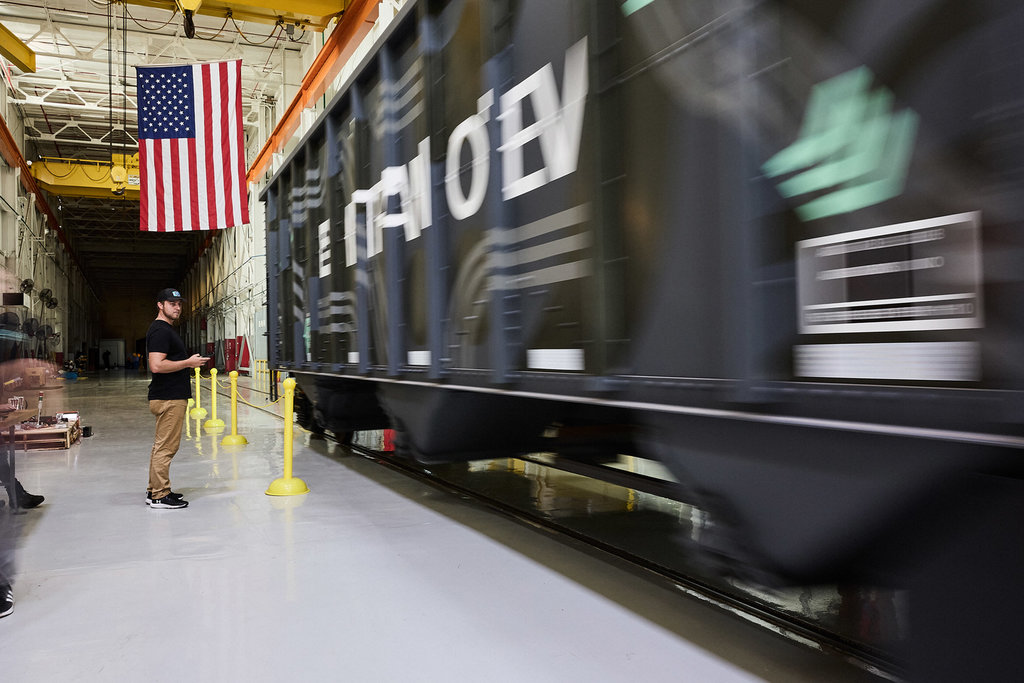
If you allow for let's say, an 18% conversion of the rail cars to ReVolts, which is still a loaded car just like a TugVolt, you'll save 20% of your emissions right off the bat. The way that that works is similar to distributed propulsion systems in normal trains in North America with multiple units.
What we do is get the main command from the engine, and then we’ve built a mode for this vehicle that runs like an eBike, where the electric motor kicks on and starts pushing, taking load off the engines. And then when it tries to brake preferentially, it'll try to recharge the battery packs as opposed to losing that braking energy as heat.
Peter Nilson: How does the fully autonomous operation work exactly?
Timothy Luchini: So... we've got a lot of sensors on board! You've got your radar, camera, multiple GPSs, accelerometers, gyros, and thermal management systems. All those sensors are coming together and being fused to give the vehicle a perspective of what the world around it looks like.
And then we also train the vehicle to the specific routes that it's running. So we're running from point A to point B consistently and we can observe that journey. So then, within the bounds of those observations and where we know that it can operate safely, the onboard system can then take over and run those routes on its own.
Generally, it comes down to lots of sensors onboard and lots of computations taking place. And then it's using those sensory inputs together to run point to point from where it is to where it needs to get to.
Peter Nilson: The main application that comes to mind is freight, which you’ve alluded to. You have had some early success in the mining sector, does that seem like the perfect use for this tech?
Timothy Luchini: Yeah, mining is a really good market for a few reasons. One is that it's remote, so workers are generally hard to get in the first place, meaning an autonomous solution helps.
It's also easy for us to do a business case analysis. Our customers in mining are generally publishing how many tonnes of material they are moving from point A to B, and how much it costs them. If we know that information going into things, it helps us size the market to go after. And on the routes that they're running, they're making a lot of frequent material moves. They need to move a lot of material and the more diffuse the mineral, the more material they have to move to then get to a concentrating facility.
Those routes also generally don't have a lot of interaction with public crossings and things like that, and they're usually insular. What that means is the US Federal Government has deemed sections of routes insular, which means they're isolated from the rest of the network and are not regulated in the same way that interchange-connected routes are.
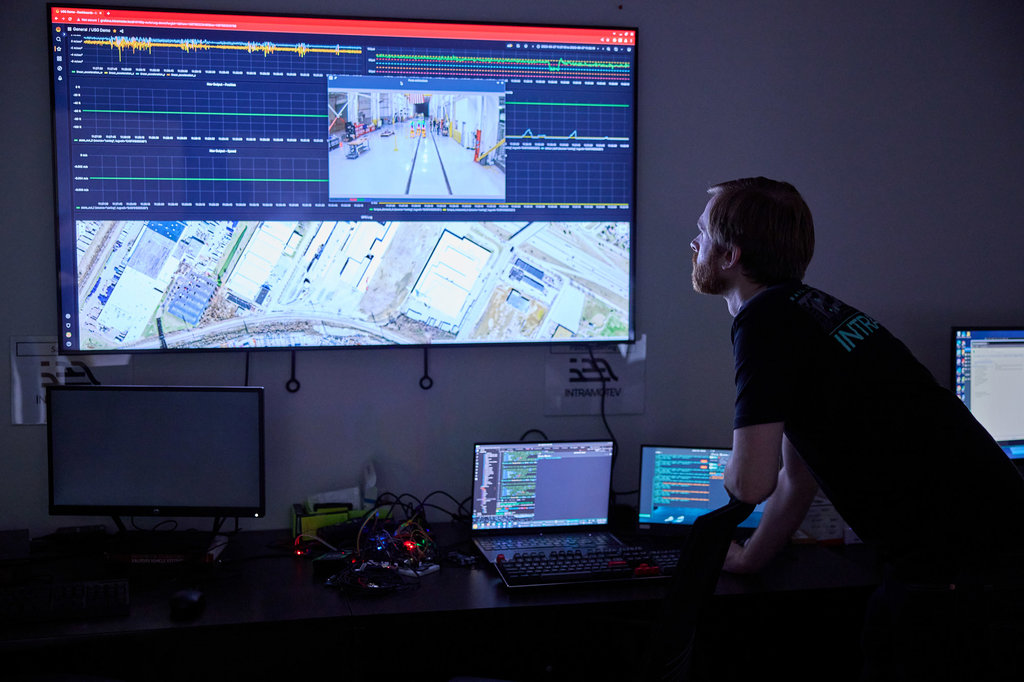
So for our first sets of use cases where we're running a lot of material consistently point to point between an A and a B location. Mining customers need to have that material move flexibly, like a truck, and they need to continuously run their processing centres. We've shown those customers that they can save anywhere from 30%-80% of their operational costs and the strength of total fleet size.
So if you're looking at an engine and 100 cars for a train moving 60 miles, you can do that with 30 TugVolts. In the case of a unit train running today, if they want to keep running it like that then they can use it in ReVolt mode.
When we were running studies with a lot of these diffuse heavy metal miners, they were telling us that they can now mine less mineral-dense deposits for an extra 10 years, because it's so much less expensive to move the materials using TugVolt or ReVolt.
And then from there, we step into the broader market. And that's really where you might expect the more traditional North American freight trains getting broken down into yards and things like that, but that's the next step for us as a company.
Peter Nilson: I can imagine that as part of that next step, when you're trying to appeal to more use cases, you would be considering licensing the technology out ot others.
Timothy Luchini: Yeah we would. We're open to various different business models and different paths, especially when we start to look at markets that we wouldn't necessarily be present in.
For example, Europe has a whole different set of things that are driving needs in rail, but actually, it's kind of interesting, where we might have a mile or two long intermodal trains here in the US, you might have 10 cars moving at different places in Europe trying to fit between passenger schedules that have priority.
You can't fit a North American-style freight train in between those passenger schedules, but you could fit two or three TugVolts or something like that. And in those scenarios, trying to understand those markets we would definitely be partnering and looking for the right types of arrangements that everybody can win and benefit from.
Peter Nilson: Are there any obstacles that you can see in the future development and rollout of autonomous electric rail freight?
Timothy Luchini: From the cost perspective whatever the business case, it's very positive. When you're looking at the net present value cases for our solution compared to a traditional train or trucking, we generally beat all of those.
From a regulatory perspective, the world has not caught up to where the technology is at. When we're trying to deploy these things and build a business off of it. These insular use cases and things like mining are really exciting because that's a space for innovation. However, that is a space where we are working with regulators to try to bridge that gap and work through waiver processes and things like that as we wait for full regulations to come online.
And then there’s the safety element, it's first and foremost in our mind every day. From our perspective, these systems will ultimately be operating more safely because of how much data is being collected and how much can is automatically being done in the background, all the standard types of things that the human brain would just get tired of constantly looking for, the computer doesn't get tired of.
Similarly, with things like bearings. How do you tell if one's good or bad? They fail very quickly. However, when we're driving them and we have results, we have data coming off a motor controller or when we have, thermal systems measuring that then we can suddenly know and predict when that is about to go bad and try to prevent it. And if it fails, it fails safely. One of the ways to do that is smaller trains. Our vehicle can start and stop on the order of magnitude of a semi-truck. It's a game-changing technology stack that we can bring to market.
Peter Nilson: What does the charging infrastructure look like for the trains?
Timothy Luchini: Charging infrastructure is a big question and a challenge. One of the things that helps us is the smaller total battery pack. If you want to go a further range, we just suggest that you add more of these together. It's like adding more batteries to a flashlight, except now we're platooning these vehicles so physically they can share energy between them.
We have tried to electrify and add batteries to a full locomotive. You end up with 8 megawatts (MW) of batteries on a traditional diesel-electric locomotive. That is an enormous challenge for charging infrastructure! Where do you get 8MW at once and charge it in a reasonable time? The way that we have designed our system, is it has an onboard charger and it only has about 100 kilowatt hours of power in the smallest version of it.
In general, the charging infrastructure requirement is a local AC power connection. Generally higher power is better for 80MW-40MW. We could charge at 120MW, it just takes longer and a higher current draw. We could charge in six to eight hours with the onboard charger and then with dedicated infrastructure local charging, you can get that down to about 30 minutes. That is more of an investment on the customer side of things.
So if they run 24/7 operations, then that makes sense. If they're running one or two shift operations then we've designed it to be able to charge in that third overnight shift timeframe.
Peter Nilson: What does the future hold for Intramotev? You're still testing the technology, but are there any milestones that you want to hit in terms of expansion or research?
Timothy Luchini: For sure. We have a huge list of expansion goals, research goals, and things we want to work on and expand into. Our first and foremost goal now is supporting our current customers. We're deploying six vehicles between two customers currently, both of which have dramatic expansion opportunities should they want to.
That's the focus with the current resources and team and then we'll be looking at taking out another 10 customers here. From there each has anywhere on the order of two to three to 10 vehicles apiece. They are early tech adopters, so we need to be supporting that.

From there we'll be looking to expand and bring in more customers. We’re looking at taking another 10 customers, each having anywhere between two or three to 10 vehicles apiece. In turn, we'll be hiring another 15 engineers here in the next couple of months and continue to hire from there. And then obviously, the resources for growth. So we are reinvesting in our company aggressively and we'll continue to do so. bringing in outside and strategic partners along the way for that.
I think that the technology for this is here, it's ready. It functions and it works. I don't see a future where this doesn't exist. So that's exciting, as we bring this forward and think outside the box a little bit with the context of rail.