Cover Story
Keeping the circular economy on track
Keri Allan looks into the circular economy in the rail industry, be it reusing old rail materials, changing design philosophies, and the financial considerations for raising sustainability in the sector.
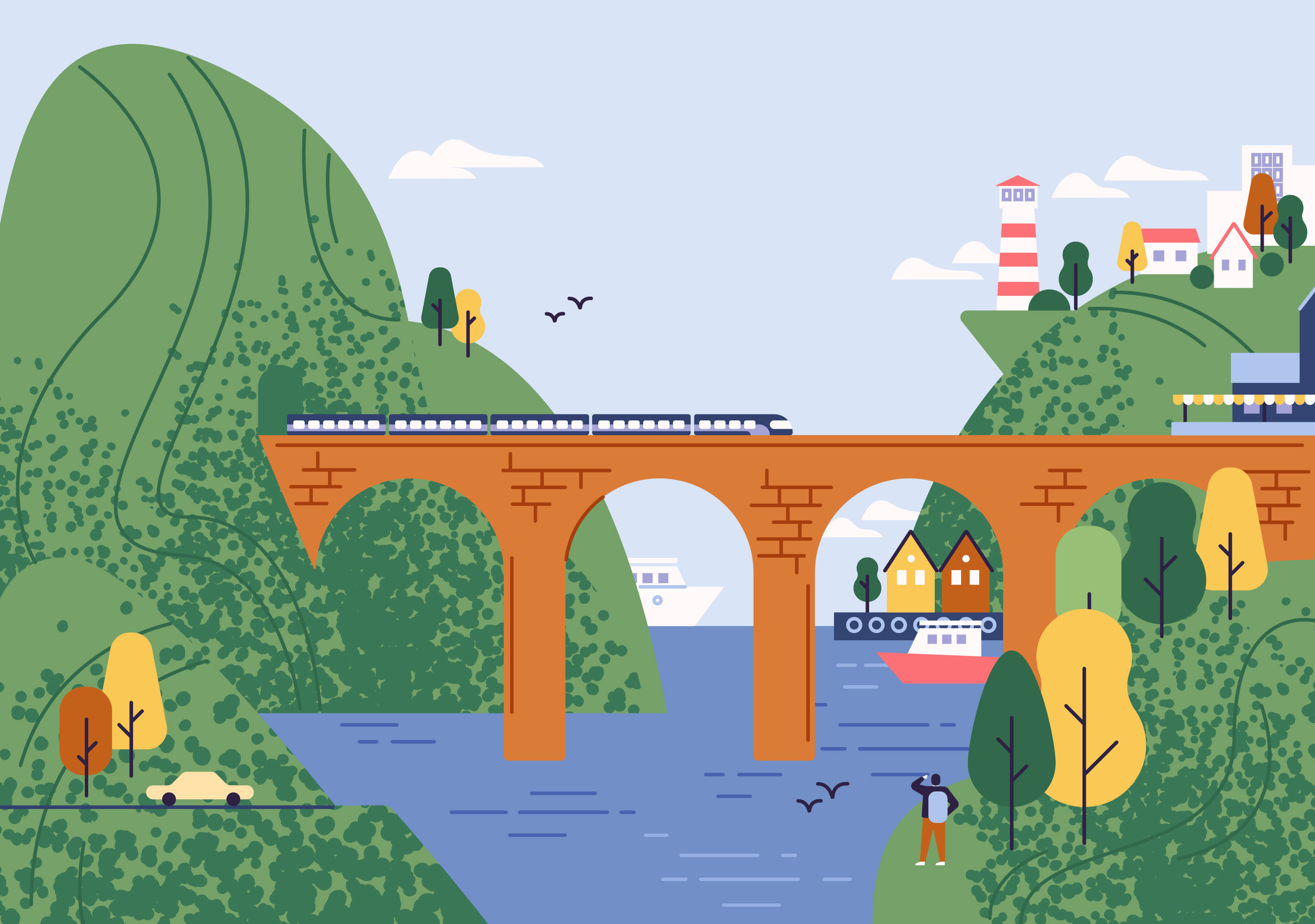
Render of the West Yorkshire mass transit system tram passing through Leeds City Centre. Credit: West Yorkshire Combined Authority
The concept of the circular economy is becoming more commonplace in the rail industry, from designing for reuse and minimising waste, to the preservation and repurposing of existing infrastructure.
Top-down policy direction and national commitments to net zero are driving this shift, meaning organisations must consider ways in which their climate and environment impacts can be reduced.
These considerations are often baked into project requirements and processes, for example in requirements to assess whole life cost and embodied and operational carbon, notes Chris Mills, senior director at ChandlerKBS, the infrastructure division of Cumming Group.
“These incidents are referred to as wrong side track circuit failures (WSTCFs), which compromise system integrity and could result in a train collision or derailment,” says Ben Altman, senior research analyst at the Rail Safety and Standard Board (RSSB).
Lifecycle thinking from the design stage
Larger organisations have gone so far as to appoint dedicated circular economy strategy managers, including Network Rail. Katie Beardsworth sets the organisation’s strategy in this area, identifying workstreams that are needed to achieve that and working with the business to understand how they’re going to be delivered. Within an organisation like Network Rail, she says the circular economy falls under two levels: business process and materials.
“I ask how we are embedding circular requirements into our policies, processes, standards, and design guides; so that when we’re designing something, we’re doing so for modularity, durability, and circularity,” Beardsworth explains. “Obviously, we use a lot of materials at Network Rail, so they need their own circular journey. So, we look at how we can make each of our key materials – like ballast, sleepers, clips, and wire – more circular.”
Between these two levels sits the procurement process, because Beardsworth sees circularity hinging on getting procurement right. “We look for materials that are either made, or we can use, in a circular way,” she says.
When it comes to undertaking infrastructure projects, experts advise that circular thinking is integrated from the start. For example, architects and designers are approaching rail infrastructure with modularity and flexibility in mind.
A notable example is the modular platform roof system designed by international architectural company gmp Architects for Deutsche Bahn. This design integrated essential functions such as weather protection, lighting, audio systems, and passenger information displays into a single element and has been implemented across numerous German stations.
“The modular nature of the system allows for elements to be reused or relocated, offering sustainability benefits if a station is ever decommissioned. Furthermore, repetition of modular components helps reduce costs and accelerate construction,” notes Tobias Keyl, an associate partner at gmp Architects.
Circularity of materials
At the highest level, circularity focuses on infrastructure, while at the other end of the spectrum, it’s about the reuse and recycling of materials. Many infrastructure managers continue to look for ways to improve this, with one great example coming from Network Rail’s project to improve the circularity of one of its most common materials – ballast.
Historically, none of the ballast removed from its network was reused, but a supply disruption forced the organisation to rethink. Partnering with the University of Southampton in the UK, tests revealed that blending used ballast with new – at ratios up to 50:50 – not only met safety standards but slightly outperformed virgin material.
This discovery led to a pilot scheme with Land Recovery, a supplier of primary and recycled construction materials, which now washes, screens, and blends spent ballast for reuse. Though currently limited to a few locations, a 2027 tender for a new national contract will require bidders to offer this blended product.
“Once scaled, we expect to save around half a million tonnes of new ballast and £1m annually,” says Beardsworth.
The business case for circularity
While discussions around the circular economy understandably focus on sustainability, the financial benefit of embracing circularity is often overlooked.
“There’s certainly still education needed about the total lifecycle benefits of circular products,” says Tim Noonan, CEO and founder of Evertrak, a US-based manufacturer specialising in composite railroad ties. “Many decision-makers are familiar with the upfront costs, but less aware of the significant operational savings and extend service life such products offer.”
In addition to a lack of understanding around the business benefits of circular thinking, there are other factors that may hinder its adoption. For example, high speed rail infrastructure can have complex technical requirements, particularly related to structural and fire safety, security and operational performance, which can often limit the feasibility of reusing materials in new construction.
Additionally, uncertainty surrounding the reliability and certification of reused components further complicates these efforts
Tobias Keyl, an associate partner at gmp Architects
Even so, every project presents opportunities to enhance circularity in some form, and the next major challenge for organisations is to ensure these initiatives go beyond tick-box exercises and become measurable, impactful efforts that are continuously improved.
Some organisations, such as Network Rail, are using circular economy metrics to measure the impact of their initiatives.
However, even Beardsworth admits these are relatively basic, revolving around the amount of material reuse and waste. However, her goal is to implement something more advanced in the coming years.
“We’ve done some research on a tool by the World Business Council for Sustainable Development called the circular transition indicator (CTI) and I’m aware that some rail organisations in Europe are using this as a measure, as it gives you a percentage score of how circular you are as a business,” says Beardsworth.
“At present, we’re still too far from being able to report in a way that would enable us to yield meaningful insight from this, but the goal is to eventually use the CTI, or a similar tool, to gain a comprehensive view of circularity across the entire company.”
Laying the track for a circular future
The rail industry has always been cautious of embracing new technologies and ways of working, but it’s clear that big steps are being taken to improve circularity across the industry.
Mills believes further standardisation will help to bring greater transparency and a clear picture of how projects are performing, and that good governance will be crucial to this.
“As a business we build governance and feedback mechanisms at the outset, so we can continue to challenge a project on its delivery against the circular economy principles, but this isn’t necessarily something that’s done industry-wide. As it stands, circular economy thinking is too often delivered project by project, where what’s needed are broad overarching principles that can be taken up by the industry as a whole,” he notes.
“We have a patchy approach, with some projects performing better than others, different budgets failing to talk to each other and best practice being lost. I think the establishment of GB Rail brings real opportunities here, as having a centralised body enshrining these principles from the top down and creating the space in which supply chains can grow and businesses are confident to invest, could really move the dial on.”
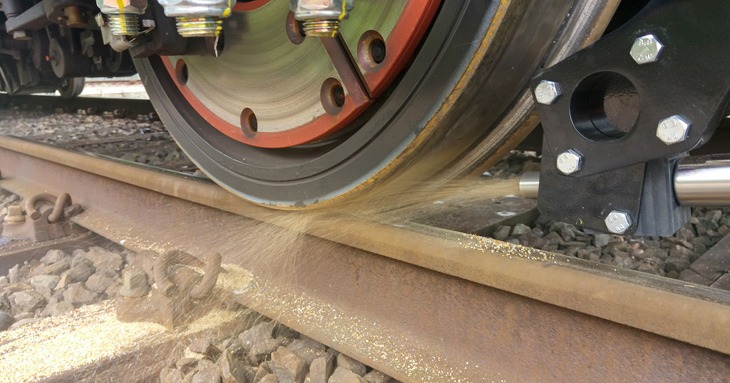
Sand particulate is a common material used to manage rail adhesion. Credit: RSSB
The mine’s concentrator can produce around 240,000 tonnes of ore, including around 26,500 tonnes of rare earth oxides.
Gavin John Lockyer, CEO of Arafura Resources
Total annual production
Phillip Day. Credit: Scotgold Resources
Production challenges for rare earth supply chains
There are two key issues with the production of REEs. First, all the rare earth deposits are mixed together, so it is difficult and expensive for processors to separate them and to take advantage of their individual properties. It is similarly challenging to split up the more valuable ones, such as terbium, from those of little value, like lanthanum.
Second, REEs are bound up in mineral deposits with the low-level radioactive element, thorium, exposure to which has been linked to an increased risk of developing lung and pancreatic cancer.
These obstacles create a huge challenge for any Western company that wants to become involved in the industry. However, they must be overcome if the Western world is to end its dependence on China.
Caption. Credit:
The biggest rare earth mines are located in China, and this source of domestic production has helped drive Chinese dominance. The Bayan Obo deposit in Inner Mongolia, north China – containing 40 million tonnes of rare earths reserves – houses the world’s largest deposits. The mine has been in production since 1957 and currently accounts for more than 70% of China’s light REE production.
However, Western mines are aiming to change this balance of production and power. The Mountain Pass Mine, owned by MP Materials , a Las Vegas-based mining company, is an open-pit mine of rare earths on the south flank of the Clark Mountain Range, 85km south-west of Las Vegas. In 2020, the mine supplied 15.8% of the world’s rare earth production and is the only rare earth mining and processing facility in the US.
In October 2020, Donald Trump, the former US president, signed an executive order declaring a national emergency in the mining industry, aimed at boosting the domestic production of rare earths. Trump ordered his cabinet to study the matter, with a view towards giving government grants for production equipment and imposing tariffs, quotas or other import restrictions against China.
The move, it said, would “allow the US Government to leverage the resources of its closest allies to enrich US manufacturing and industrial base capabilities and increase the nation’s advantage in an environment of great competition”.
The move, it said, would “allow the US Government to leverage the resources of its closest allies to enrich US manufacturing and industrial base capabilities and increase the nation’s advantage in an environment of great competition”.