Cutting down trees
In the age of steam, lineside vegetation was cut back as far as possible to prevent an errant spark from setting Britain’s fields alight. However, in today’s landscape of diesel and electric locomotives, trees and shrubs are flourishing next to the railways – a boon for those distressed at the sight of chunky locomotives passing by, but a nightmare when it comes to falling leaves.
Network Rail has expanded its vegetation management practices and says it uses a number of methods to ensure its tree cutting practices are in line with environmental standards. Nevertheless, large-scale operations to cut trees even further from the rails will always come under fire from more ardent green organisations.
After The Guardian alleged earlier in 2018 that Network Rail was set to commence a ‘secretive tree felling operation’, a petition calling for the infrastructure owner to stop chopping down millions of trees attracted more than 100,000 signatures. This prompted the UK’s Department for Transport to launch a review of Network Rail’s vegetation management practices.
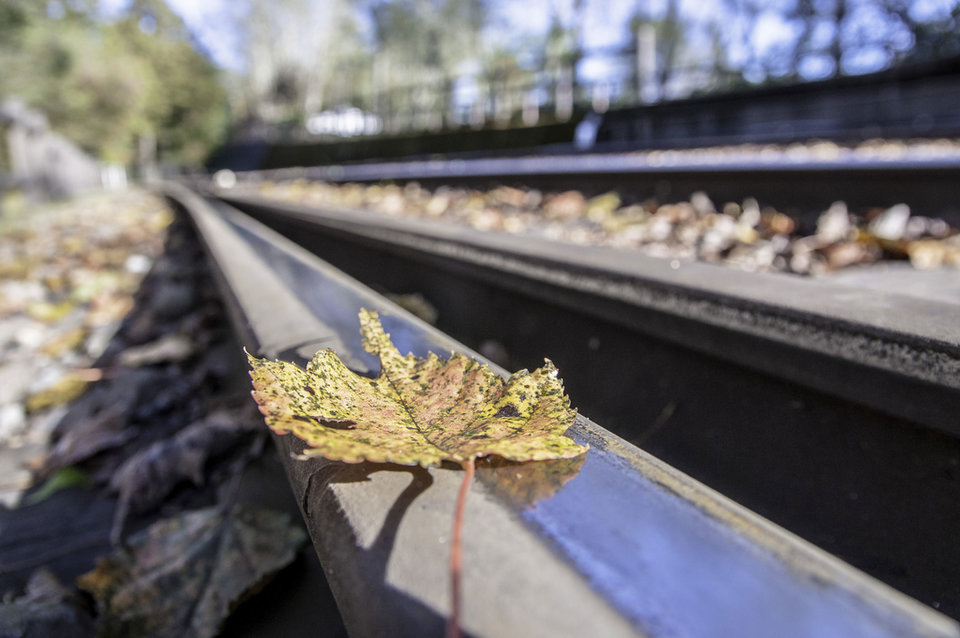
What-er solution!
Many operators have opted to take on the fight to the leaves, deploying small armies of trains equipped with high-pressure water jets to blast shrubbery into oblivion.
This year, Network Rail went hell-for-leather, dispensing a record 61 leaf-busting trains onto the railways. The trains are equipped with water jets that are so powerful they can reportedly cut through steel and will travel a distance spanning more than four times around the world on the UK’s South-Western rail network during the autumn months.
After spraying tracks with water, the trains lay down an adhesion modifier – a composite material of steel shot and sand suspended in a gel-like substance – which improves rail adhesion when it dries.
Making sanders sandier
Aside from specialised gloopy composites, sanders can be fitted onto locomotives to apply a fine layer of dry sand onto tracks across the year. According to representatives of the Rail Safety and Standards Board (RSSB), it’s a process that could be significantly improved by the introduction of new sander technology.
In the past, many trains have been equipped with ‘fixed rate’ sanders, which methodically blast sand between wheels and rails at certain points on the track. However, the RSSB has been exploring the use of double variable rate sanders (DVRS), which automatically apply more sand when braking at higher speeds. By optimising this process, it claims, trains could see their stopping distances halved.
The RSSB has carried successful research with DVRS in 2017, finding that the new approach “dramatically reduced braking distances in poor adhesion conditions, and provides assured 6% braking performance”. At the end of 2018, the organisation was trialling the new sanders in the hope that they could one day eliminate adhesion-related platform overruns and the need for specialised autumn timetables.
“We are using the data collected in 2018 to better understand the causes and effects of low adhesion and how to maximise the benefits DVRS offers in order to efficiently demonstrate this to industry in autumn 2019,” reads a statement compiled by RSSB experts.
Cryogenic pellets produce ‘shocking’ results
The RSSB says that although DVRS is a “significant step change in its fight against the leaves on the line issue”, it is just one of a number of technologies that could be explored as a way of combatting low adhesion.
One direction could be finding better alternatives to sand as an adhesive. In Japan and Taiwan, freight locomotives have been equipped with Cerajet – a composite made up partly of ceramic substances that can withstand much higher forces than normal sand – to break down leafy residue on rails.
Another suggestion explored by RSSB has been the use of cryogenic pellets, which could be used to shock the slippery leaf layer and cause it to crack and de-bond. As well as leaving no residue behind on tracks, the added benefit is that the pellets are non-conductive, meaning that they aren’t as dangerous to use in a rail environment as water-based solutions.
Magnetic braking systems
Wheel slide protection systems – which operate in a similar way to anti-lock braking systems on the road – are now a standard application onboard many modern trains. However, RSSB research has been working towards finding other innovative braking solutions for the problem.
Magnetic track brakes, for example, are already being used in a number of European systems. These essentially consist of a brake mounted in between train wheels, which when lowered to the rail uses a magnetic clamping force to cause deceleration.
According to the RSSB, research has shown MTBs are compatible with infrastructure in the UK, and could "contribute to assured stopping capability".
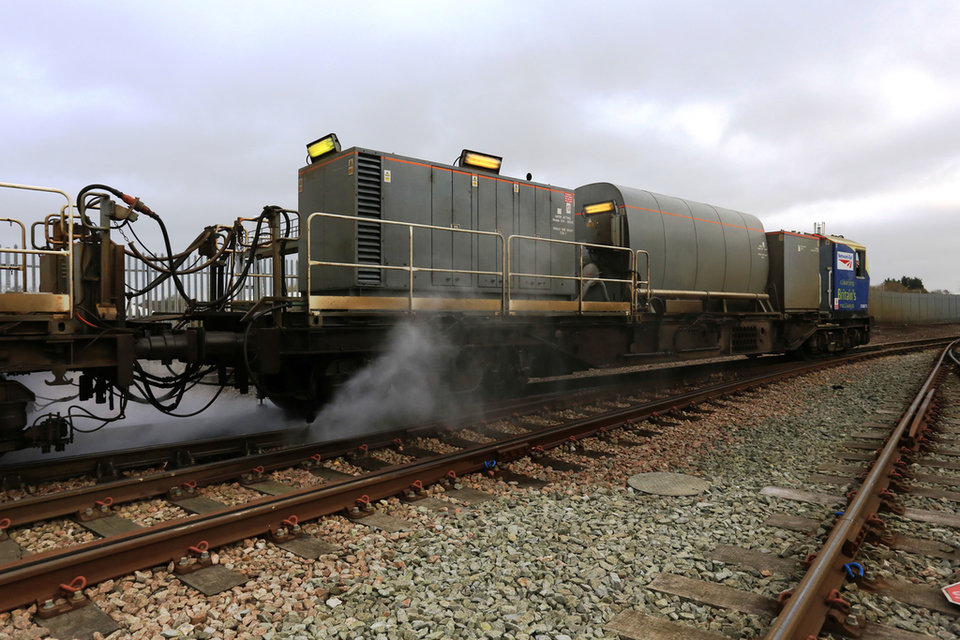
Image: Peter Selway / Schneider Electric
Smart sensors
If there’s a problem that needs solving in the modern world, it’s a safe bet that a ‘big data’ or ‘smart’ solution is around the corner, and cleaning up slippery leaf mulch on railheads is no exception.
In 2016, University of Birmingham professor Lee Chapman developed a prototype for a new smart solution called AutumnSense. The idea is that the system would use low-cost sensors to keep a constant lookout on moisture levels across the railway line, thus allowing rail operators to help forecast when clean-up operations across the line.
“One of the major issues with road and rail safety is that hazardous conditions are usually highly localised,” said Chapman in a press release. “For remedial actions to be efficient and demonstrate ‘best value’ for the taxpayer, resources should be deployed where they are needed, rather than in a blanket fashion.”
The sci-fi approach
Taking a more ‘Star Trek’ approach in 2014, Dutch railway company Nederlandse Spoorwegen (NS) explored the use of train-mounted lasers, which are focused at a strong enough wavelength to pulverise leafs and organic debris, but weak enough that they reflect off rails.
The idea was first conceptualised in the early 2000s, when Royal Navy Lieutenant Malcolm Higgins set up a new company, Laser Thor, to develop a state-of-the-art railhead laser cleaner. The final product comprised of two lasers, which channelled 5,000ºC pulses of light into leafy mulch, causing it to expand and rise off the rails.
Initial trials with Network Rail were positive, but found limitations – in particular, that it became difficult to focus lasers correctly on tracks when the train moved at higher speeds. An NS spokesperson was asked about the outcome of its 2014 trial, but did not reply – and it seems that the concept of ‘lasers on the line’ could now be in limbo.
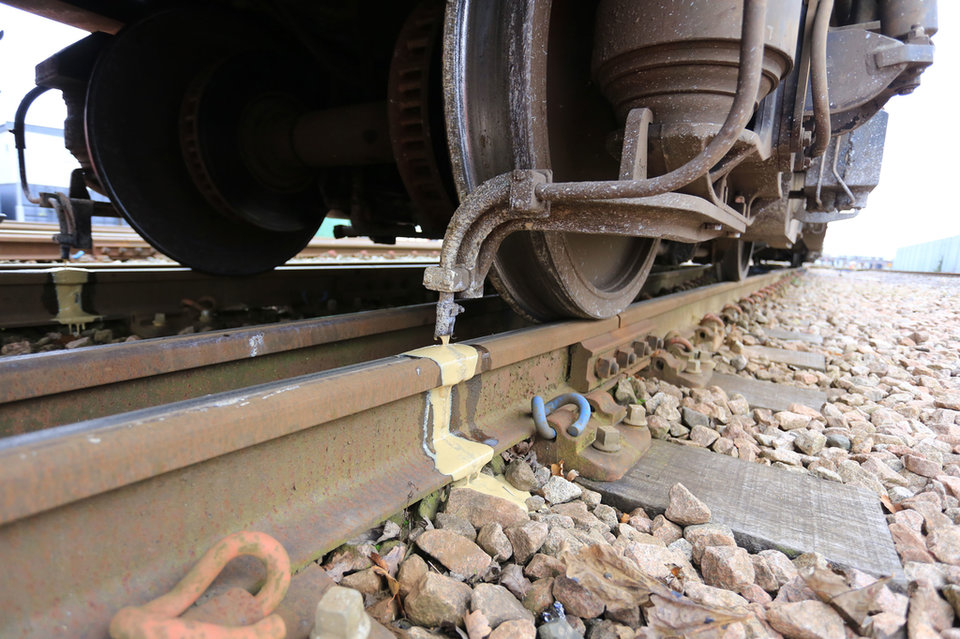
Image: Peter Selway / Schneider Electric