Company Insight
Sponsored by Goldschmidt
SAFETY IS MEASURABLE
Measuring & testing solutions from Goldschmidt: smart inspection for enhanced safety and quality of your rails
A
detailed diagnosis of the track condition is the basis for predictive maintenance, which guarantees the long-term economy and reliability of your track infrastructure.
Measuring and testing technology on inspection trains, trolleys and hand-held devices from Goldschmidt enables you to carry out detailed evaluations to identify deviations and take preventive maintenance measures.
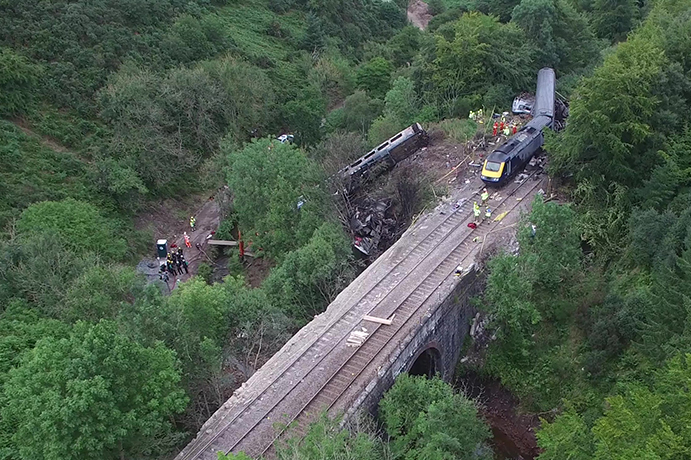
Aerial view of the derailment. Image: UK Government
ORIGINAL THERMIT®- THE BEST CHOICE FOR YOUR RAILWAYS
Around the world high speed trains, freight trains, heavy haul trains, trams and subways glide smoothly over continuously welded track. As the inventor and global market and technological leader in the field of Thermit® welding, for over 125 years, Goldschmidt has set standards for continuously welded track. The Original Thermit® welding process enables continuously welded rails of different profiles and grades. Goldschmidt develops, produces and supplies all associated equipment, machines and materials. In addition to the Original Thermit® portion, the portfolio includes, for example, refractory moulds, crucibles and devices with a digital interface. You also benefit from the on-site services at the track construction site thanks to well-trained and efficient welding teams.
Reliable, safe and efficient infrastructure through innovative testing technology for automated rail testing
In order to ensure rail traffic safety, it is vital to have precise knowledge of the condition of the track infrastructure. The subgrade, superstructure, switches, rails and overhead line form an overall complex in which individual components influence each other.
The inspection and analysis of the condition of rails is a prerequisite for condition-based and preventive rail maintenance – which in turn is a prerequisite for the sustainable reduction of lifecycle costs of railroad infrastructure components.
Against this backdrop, two innovative Goldschmidt Group companies, PLR from Germany and GRAW from Poland, have set out to make the inspection of rails for various types of damage safer and the reporting of results more reliable by combining their respective products. While the focus in the past was more on detecting rail defects caused by production, today it is more on operational defects due to higher axle loads and speeds. This was taken into account at an early stage in the further development of the testing systems.
The extent of the flooding and the scale of the damage is something I have never witnessed before
Requirements for the inspection of rails for near-surface defects
Many European railroad infrastructure companies have developed internal guidelines for testing rails for near-surface defects, coordinated them with their supervisory authorities and put them into force.
A European standard for the eddy current testing of rails, DIN EN 19729-2, was published for the first time in 2020. It describes how eddy current testing is used to detect and classify surface cracks in rails – mainly caused by rolling contact fatigue. The main focus is on – but not limited to – head check and squat defects.
Head checks (UIC 2223) are cracks open toward the rail surface with a high frequency per meter, which are mainly found at the running edges of outer rail curves. Head checks in an advanced stage can thus be classified as particularly dangerous rail defects.
Squats are cracks that spread inside the rail head. Since squats (UIC 227) can also occur in close succession, there is a particularly high risk of a rail section comprising several squats breaking away, which can lead to derailments.
Eddy current inspection of rails is always closely connected with simultaneous visual inspection. For a comprehensive assessment of rail damage and the search for its cause, it is essential to look at the track system including ties, fasteners, etc.
Qualified and certified personnel in accordance with DIN EN ISO 9712:2012 and EN 16729-4:2019 is necessary for carrying out the inspection activities on rails.
In recent years, the demands on inspection systems have increased due to changes in damage patterns. Available track possessions have been reduced to a few hours per day to carry out inspection and maintenance work on the track. Automated, non-disruptive inspection of the rails during regular traffic is thus becoming unavoidable. Limited maintenance budgets require software-based solutions for the efficient evaluation of the recorded condition data.
Goldschmidt eddy current and video inspection test systems
Eddy current test system
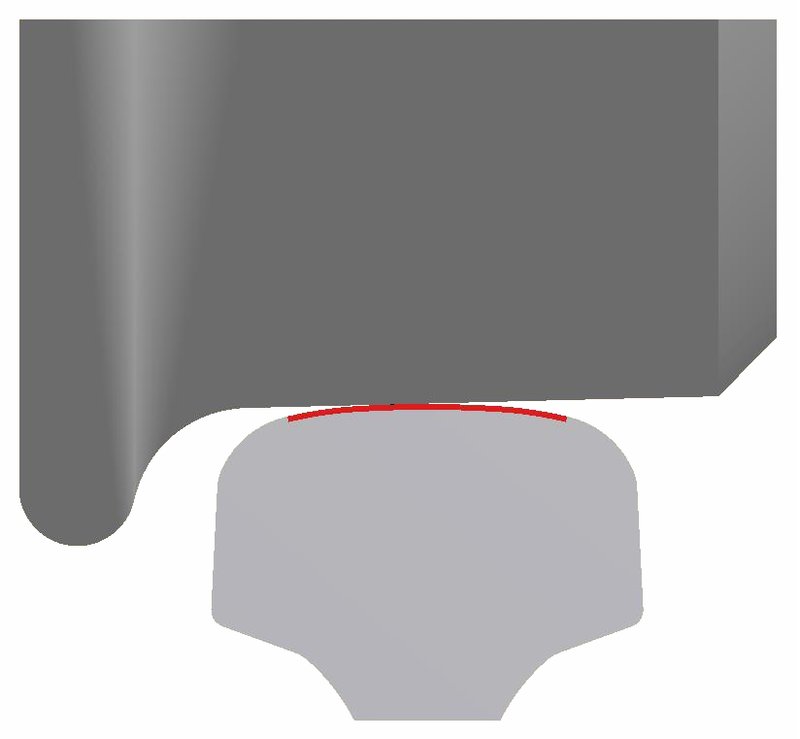
Running surface
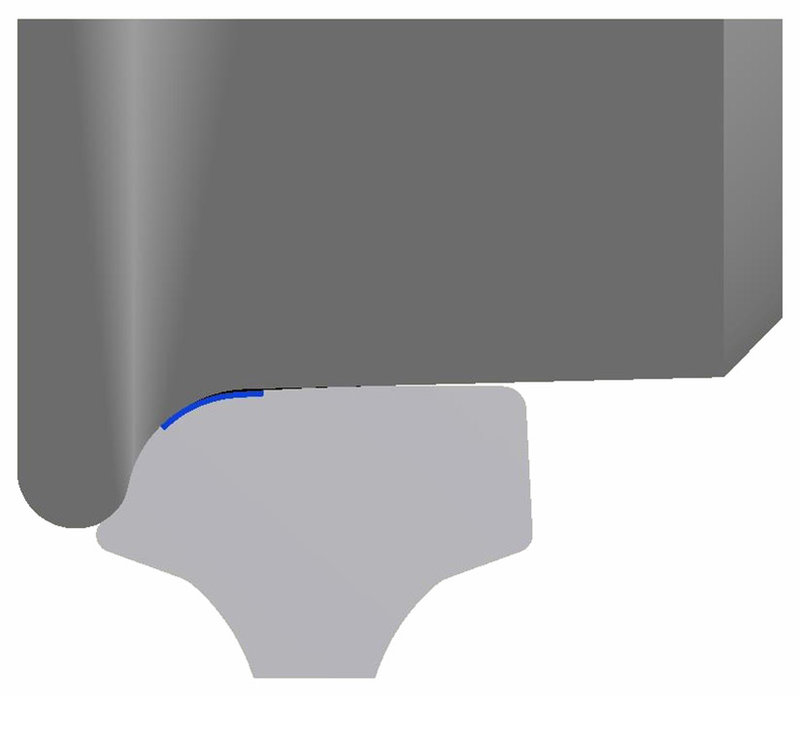
Running edge
Near-surface rail defects can be very accurately detected and evaluated with the SIS ET HS 88 system at test speeds of up to 80 km/h, with up to 8 probes per rail in a range from -45° on the running edge to +10° on the running surface.
Intuitive user guidance, precise localization and software-based algorithms make it possible to quickly generate an inspection report with just a few clicks. The report is easy to read and can be imported into other customer systems as an export file. Among other things, the inspection report provides information on crack lengths, damage depths and crack frequency in the damage areas.
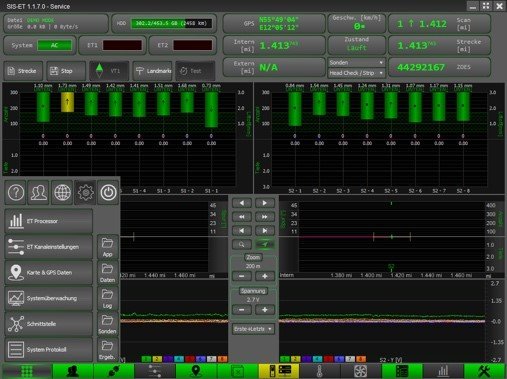
Rail inspection monitoring screen
The data is used to evaluate the actual condition and to initiate rail maintenance measures. This provides our customers with the information they need to know which rail machining process is the most economically viable solution for each use case in order to restore the rail to a flawless condition. Regular inspections make it possible to detect incipient cracks at an early stage and eliminate them before they start to grow exponentially. The result data of the SIS ET HS 88 system are an essential control instrument in the process of optimizing and extending rail service life.
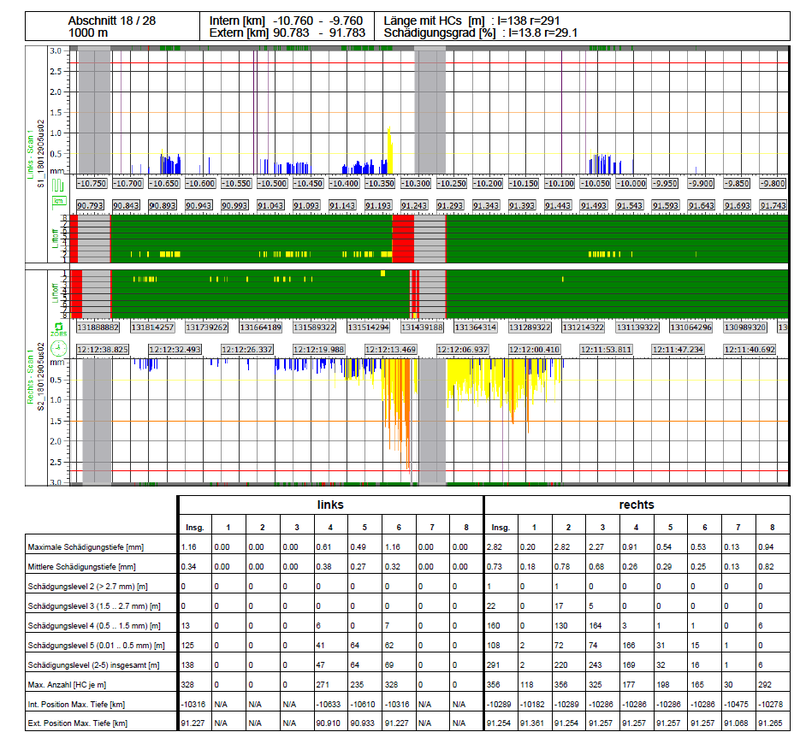
Inspection report
The eddy current testing systems are successfully used in many countries by infrastructure companies, measurement and testing service providers, as well as for rail machining service providers. They are successfully used on grinding and milling vehicles for monitoring the quality of the work.
Video inspection system
Our video inspection system recordings provide you with more comprehensive insights into the condition of the superstructure by means of continuous image recording. The video inspection system consists of line-scan cameras and powerful LED spotlights, which enable image registration in almost the same lighting conditions during the day or at night, and at high speeds. The data are automatically analyzed based on defined characteristics – using software support and integrated image processing algorithms. If irregularities are detected, e.g. cracked ties, rail fastenings or insulating joints, as pictured here, the images are registered with the corresponding location information, e.g. track ID, GPS position. These can be exported in any format.
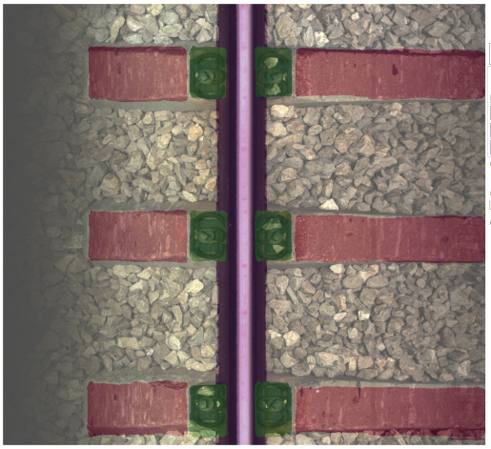
Video inspection
Strong together
Through the combined use of eddy current and video inspection systems, images of the respective damaged rail section can provide further clarification on the causes for each irregularity detected by eddy current. Rail defects which were detected previously and already secured do not need to be revisited. In addition to saving costs, the reduction of the number of employees on the track is another advantage. This makes walking along the track to detect loose or missing fasteners unnecessary – while at the same time increasing occupational safety for our customers' employees.
Shown in the picture, the eddy current inspection technology has detected a squat defect in the left rail and entered it into the inspection report. The video inspection system has confirmed this squat in its image recording. This rail defect has thus been confirmed by both systems and the inspection statement is redundant and very reliable.
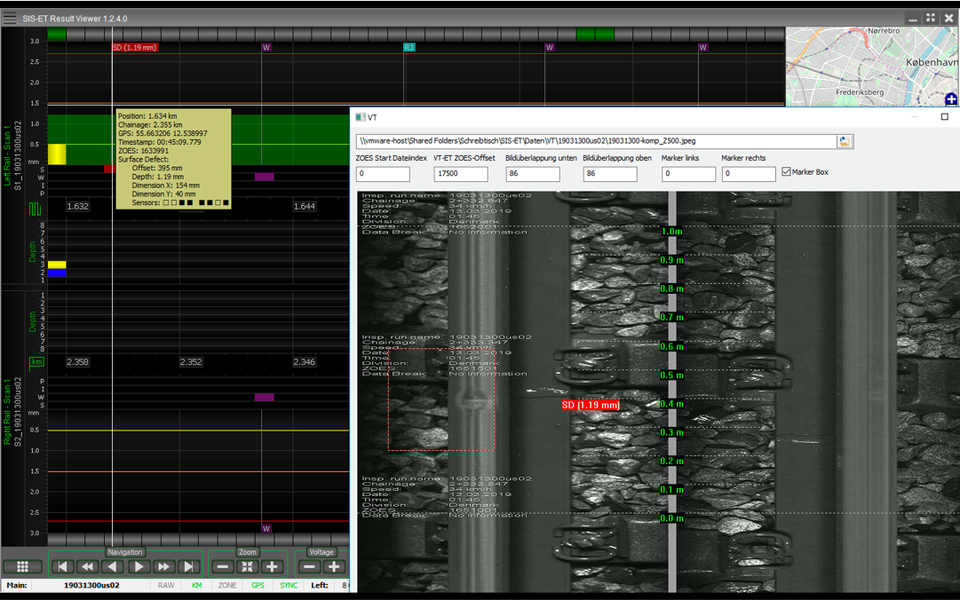
Eddy current test report with image recording for detected squat
Data management and analysis
During the measurement run of the train, position data, such as D-GPS, are stored together with the inspection data, and result files with the detected defects are created. All data from the measurement run can be transferred online to the customer's data processing center, where the data can then be analyzed and the configuration of the recordings saved.
The correct localization of the test data is also of utmost importance when it comes to comparing current test data with historical data. Automatically detectable infrastructure incidents can be added to the test data during registration in order to ensure correct positioning.
Summary
The Goldschmidt Group offers its customers measurement and testing systems customized to fit their needs for the detection of rail defects and both, track and rail geometry deviation as part of automated inspection. The combination of eddy current testing results and video inspection enables our customers to notably optimize maintenance work. This significantly helps to increase the availability of the network and to make efficient use of maintenance budgets.