The newly developed wagons from DB Cargo and VTG consume 3%–8% less traction energy.
Innovation on track: the DB Cargo / VTG research project
The test vehicles taking part in the ‘Innovative Freight Wagon’ research project were all fitted with innovative components that have generally not yet achieved a high level of market penetration.
“This includes an electro-pneumatic brake, a digital brake indicator, power and data bus wiring or quiet wheelsets with wheel noise absorbers,” VTG told RailFreight.com. “Other features, such as targeted weight-saving designs, are specific to particular wagons.”
In order to accommodate a wide range of container combinations, the intermodal wagon was redeveloped as a container wagon, with specific emphasis on a weight-optimised design, while both disc brakes and a telematics module allowed longer maintenance intervals and higher availability.
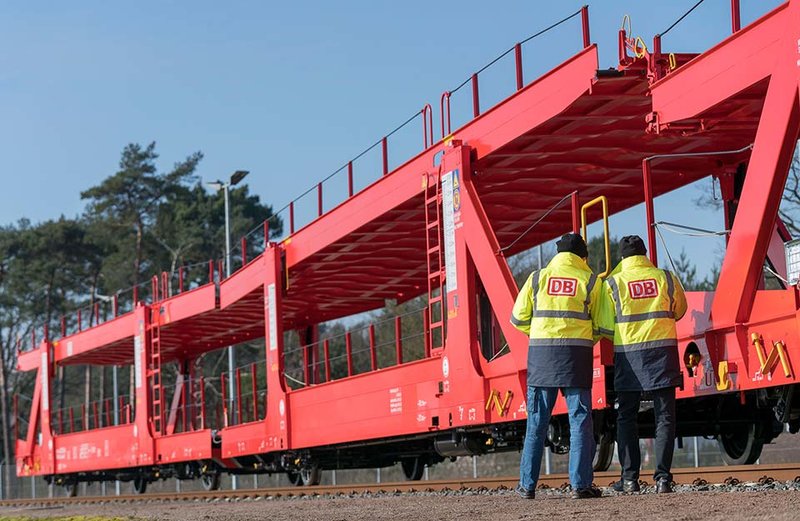
Image: The ‘innovative freight wagons’ are designed to transport steel products. Credit: DB Cargo.
The double-deck car transporter achieved a high loading efficiency, especially when transporting tall and heavy vehicles such as SUVs and vans, and also incorporates an adaptable upper loading level and adjustable elements on the lower loading level.
At 14.4m, the tank wagon is 2m shorter than existing types, while maintaining the same volume. According to DB Cargo, this allowed for more wagons per train – thanks to a larger tank diameter created from a new material – and the wagon also features lighter insulation with lower density.
IRJ reports that the six-axle flat wagon has been designed to transport steel products, and can carry both slabs and coils as well as containers, removing the need to convert it for the different loads. DB Cargo has placed an order for 300 freight wagons, which includes the car transporter wagon and multifunctional flat wagon BraCoil for steel shipments.
“We are continuing to invest in our fleet and are opting for flexible freight wagons,” said DB Cargo CEO Dr Roland Bosch. “They improve the quality of our transports and make them more economical, but they also add value for our customers.”
Next-level technology: SBB Cargo’s 5L Demonstrator
Swiss Federal Railways subsidiary SBB Cargo has released interim results from its 5L Demonstrator sustainable rail car project. 5L stands for low-noise, lightweight, long-running, logistics-enabled and life cycle cost-oriented. The four-year collaborative project began in June 2018, and since then each of the 16 freight wagons being tested have racked up between 20,000km and 30,000km.
Using its 5L demonstrator test wagon, SBB Cargo is testing six different systems – including bogies, brakes, wheelsets, measures for noise reduction, telematic applications and automatic coupling –supplied by different industry partners, with each wagon featuring a different combination.
Sensors gather data on mileage, transport capacity, radial distribution, speed distribution, running quality, applied braking energy and run-up impacts. The ultimate aim is to produce a wagon that is less susceptible to wear and tear, and reduce noise emissions by 5dB to 10dB compared with conventional trains.
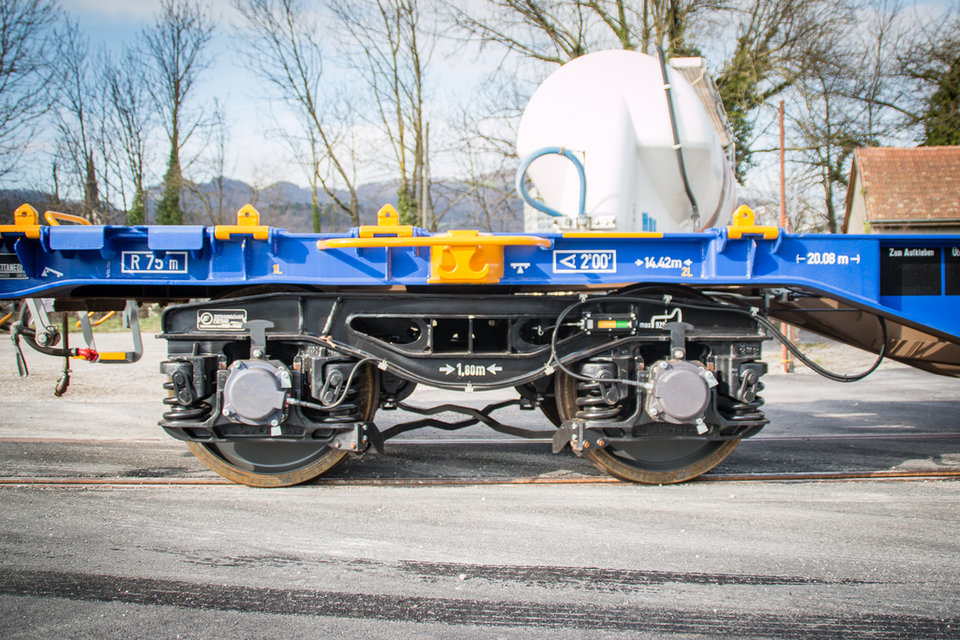
Image: The 5L demonstrator captures large amounts of data. Credit: SBB Cargo.
“The 5L demonstrator train has been operating virtually trouble-free since June 2018,” says project manager Jessica Amberg. “The measurements showed that all components achieved good to very good results in all combinations.”
“The trial operation lasts a total of four years, with a mileage of 100,000km per year,” she adds. “As soon as the necessary approvals have been obtained, the 5L demonstrator train will also be operating in Germany and Italy. This will result in longer distances and more travel time, which will lead to more meaningful measurement results.”
SBB Cargo also showcased its ‘5L next’ freight wagon – part of a project to test a new range of innovative components – at the Transport Logistic 2019 trade fair in Munich in June.
The 5L demonstrator train has been operating virtually trouble-free since June 2018.
Traxens’s Digital Freight Train uses the internet of things (IoT) to digitalise freight operations.
The Digital Freight Train
The winner of ERCI Eurail Clusters’ Coup de Cœur Innovation Award in 2018, Traxens’s Digital Freight Train – developed with Fret SNCF – uses the internet of things (IoT) to digitalise freight operations, effectively transforming conventional rail wagons into intelligent wagons capable of managing any type of asset, meaning that rail freight can be connected to the rest of the multimodal supply chain.
Based on smart devices capable of communicating with each other using a wireless digital network, the Digital Freight Train offers multiple benefits to the industry, including geolocation and arrival notifications worldwide; consignment transport conditions and status monitoring; digital assistance for loading and unloading; wagon management; and preventative and predictive maintenance.
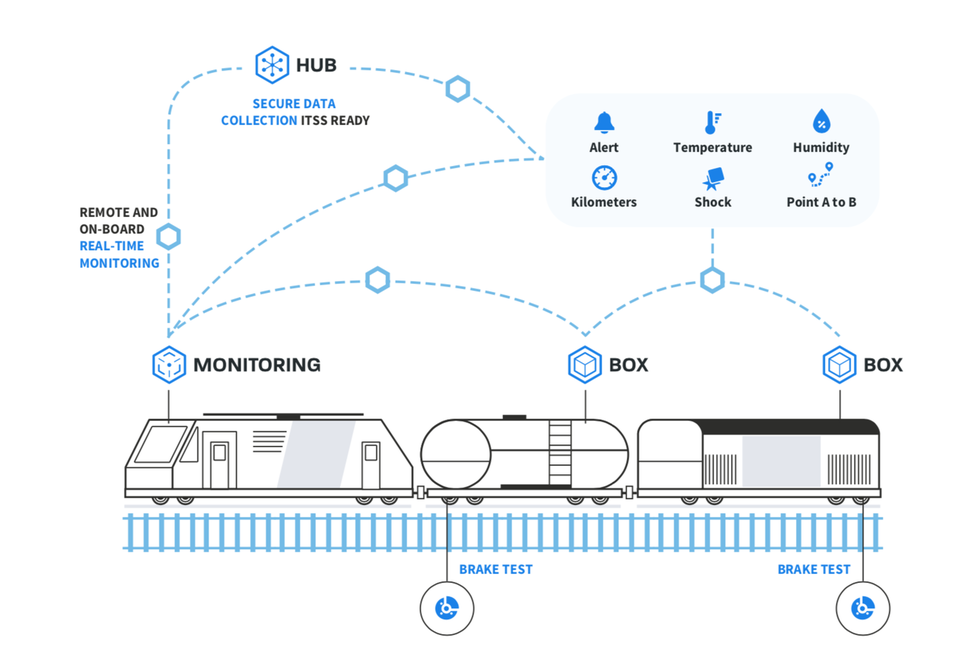
Image: The Digital Freight Train revolves around real-time monitoring capabilities. Credit: Traxens.
A significant leap forward in tank container technology has recently been achieved thanks to a collaborative project involving German chemicals giant BASF and Belgian manufacturer van Hool.
The key word here is flexibility; the new 45ft and 52ft tank containers can be transported with container rail wagons. They boast a maximum volume of 73,000l and a payload of 66 metric tonnes (double the load capacity of a typical tank container). In addition, the new tank containers can be transported on any kind of railway track and stacked on top of each other for efficient storage.
Innovations such as these provide evidence that the rail freight industry is committed to embracing disruptive digital solutions that improve connectivity, efficiency and environmental performance.