Safety
How will automated object inspections be the future of rail?
Jasleen Mann talks to Frank Van Veldhuijzen, rail innovation project lead at AutoFill, about how the company is striving to overcome inspection inefficiency within the rail industry.
T
he majority of object inspections that take place are currently conducted by people. Automated solutions, however, could provide significant support and be incorporated into existing operational processes.
Many solutions are costly and require a large amount of infrastructure. However, AutoFill’s solution combines vision technology and multisensory data which identifies anomalies in order to increase accuracy.
Tech company AutoFill aims to provide innovative solutions for object inspections. Frank Van Veldhuijzen, rail innovation project lead at AutoFill, explains the company’s vision technology and multisensory data.
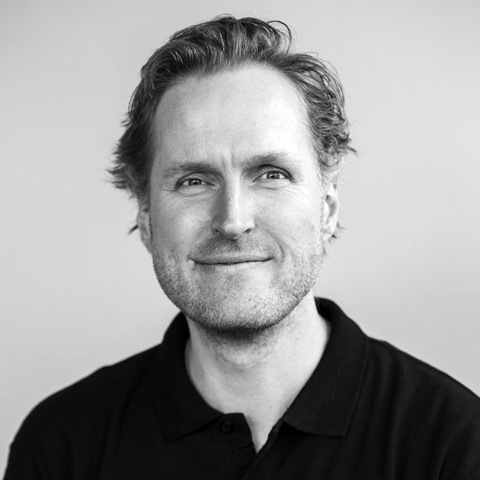
Aerial view of the derailment. Image: UK Government
Frank Van Veldhuijzen, rail innovation project lead. Credit: AutoFill.
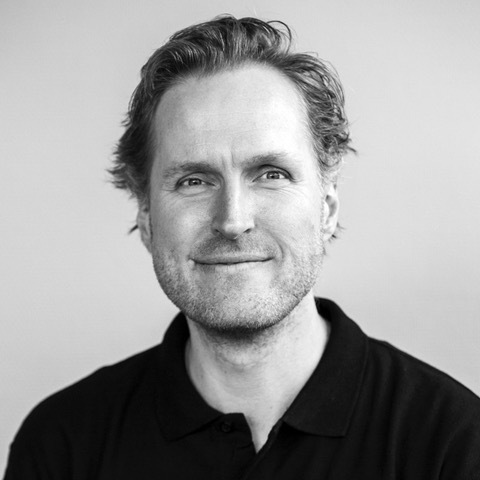
Frank Van Veldhuijzen, rail innovation project lead. Credit: AutoFill.
Jasleen Mann: How and when was AutoFill created?
Frank Van Veldhuijzen: AutoFill was born in 2019, after Gideon Richheimer, our CEO, visited some of his old customers’ sites and noticed how inefficient they were at inspecting their vehicle fleets.
He immediately saw an opportunity to address a market pain point – what if object inspection didn’t have to rely on humans?
It started out as a business theory, a complex concept (to build a lightweight, automated inspection tool with built-in multi-sensor data fusion) and turned into a successful startup, all underpinned by academic research.
One in five candidates turn down job interviews or offers due to travel inaccessibility.
What are the company’s main areas of focus?
We like to say that we have a clear eye on the far, though we focus on the near. In summary, we strive to become the worldwide standard for automated object inspections and help enterprise customers to fully grasp the long-term benefits of advanced automation at scale. We are proud that we work on the edge of what is possible and bring theoretical research to life.
Our initial focus is on FLR (Fleet/Logistics/Rail), but our technology can be applied to any market which deals with compliance-based inspections that are currently performed by humans and therefore hampered by subjective analysis.
Can you share more about AutoFill’s work with The Utah Transit Authority (UTA) and the University of Utah?
We’re currently collaborating with the Utah Transit Authority and the University of Utah on a research project into automated inspection, where we explore how to apply our highly scalable technology to inspect the federal rail system, thanks to funding secured by our partners from the US Federal Transit Administration (FTA).
Although we are still in the research phase, the results are looking very promising. This April we will visit our research partners in Utah to test our technology and detect rail defects such as damages or cracks – fully automated on a service train! After that, we will develop the technology throughout the rest of 2023 and aim for a fully operational product at the start of 2024.
How can disruption caused by maintenance work and inspections become a thing of the past?
In short, by implementing automated object inspection powered by AI and machine learning. Currently, most inspections are carried out manually, which can lead to delays – and accompanying frustrations on both customer and workforce sides.
Automated inspections can bridge this gap and enable continuous, consistent, and accurate monitoring, resulting in further efficiencies, objective reporting, increased safety and cost savings. All of this modernises, optimises and enhances quality control at scale.
The technology ensures services run on time, with any safety or engineering issues mitigated or fixed in real time.
What are the benefits of automated machine learning-powered inspections?
For customers, the benefits are simple – a more efficient, user-oriented network, providing a more reliable, flexible service.
For rail companies, the benefits are endless. For instance, through AI, you’re not limited by time. Inspections can be performed at any hour of the day, fitting perfectly to any operational process. AutoFill goes a step further. Unlike other technology providers, it can be used inside or outside, meaning it’s not dependent on weather or light situations.
AI also adds objectivity to the inspections. It doesn’t take into account weather or light, but also not mood or emotion. It is completely evidence-based. The objectivity of a report is something that is extremely valuable for creating operational consistency.
What are the challenges relating to automated machine learning-powered inspections?
Existing automated solutions are usually costly and require substantial space and infrastructure to function, as they are, most of the time, the size of a car wash facility. What makes our solution at AutoFill unique is that our entire product fits a carry-on suitcase. It weighs [next to] nothing and can be installed easily, showing great results.
It’s also worth noting that automation can only be a cost-effective solution that opens doors for reskilling entire workforces, while markedly improving customer experience and satisfaction if done right.
Having the capabilities and resources available to understand the huge volumes of data collected is imperative to the success of a project, but finding the right talent can sometimes be challenging.
What are the challenges surrounding the prevention of rail incidents?
Perhaps scepticism towards the use of automated inspection technology on rail networks.
Some decision-makers may be concerned about the cost of implementing automated solutions into their rail networks and tempted to stick to outdated and manual methods of inspection. But the cost of sticking to the status quo risks endangering lives and leads to higher financial pain later on.
No risks deserve to be taken when it comes to people’s lives. And yet avoidable incidents remain on some of the world’s biggest rail networks that could have been avoided if not due to oversights made from manual inspections that missed hazardous incidents such as faulty tracks.
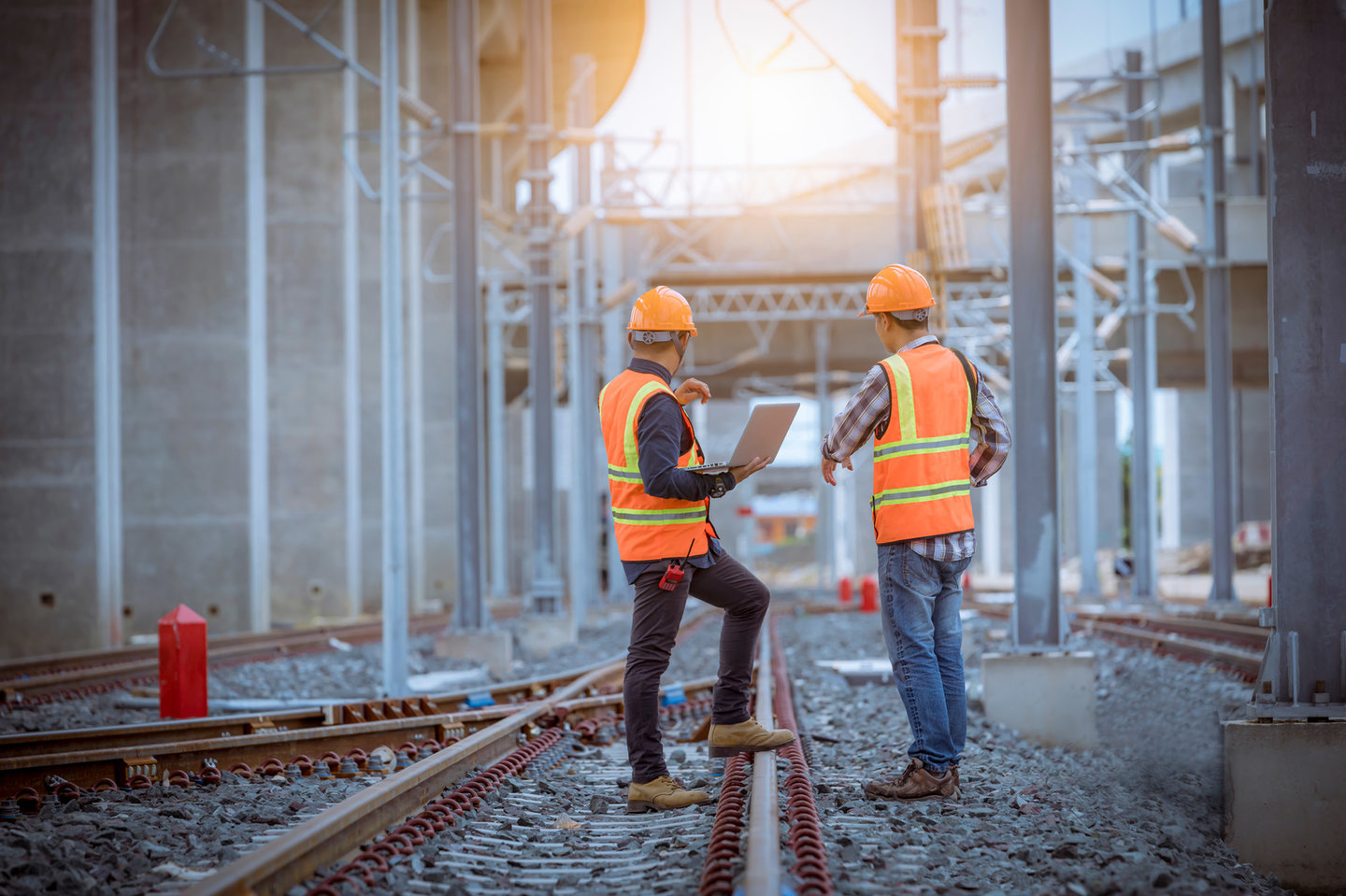
Image of Axel Schuppe. Credit: The German Railway Industry Association.
Main image: Geoff McGrath, managing director of CKDelta