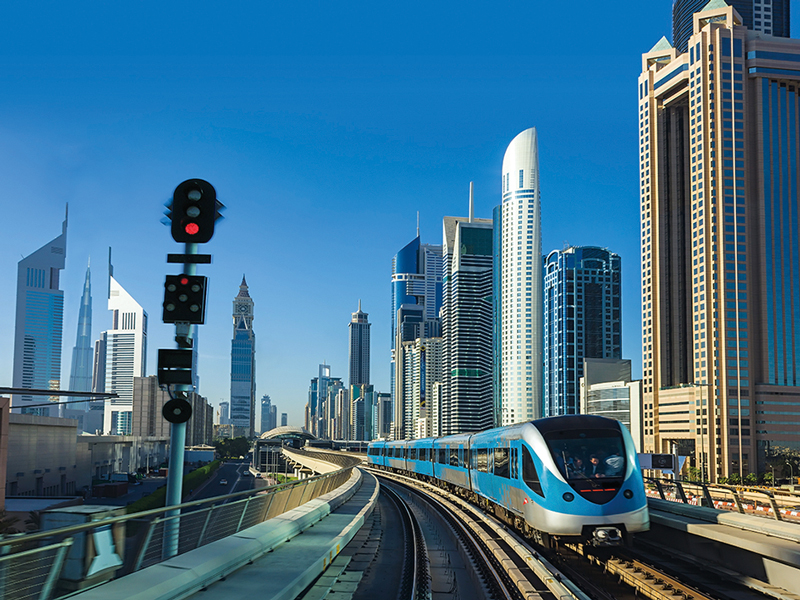
Visual Messaging System (VMS)
Wayside Sensor Integration Secures Rail Transport
VMS for Railroad Crossing System
Safety and reliability are necessary factors of a railway system. It matters large passenger capacity, high-speed transport and environment protection. Once an accident occurred, it will not only cause a major loss of life and property, but also bring a serious impact on the society. In addition, vehicles, people, animals, and accidents have caused casualties and property losses of up to millions of dollars, and once again caused people to pay attention to the safety of the road.
Visual Message System (VMS) is a smarter railway safety control solution in wayside. It integrates signal data, sensor data, video data, audio data, issue alarm, data computing, action taking, data backup and after analysis functions to secure rail transport anytime.
Key Features of Visual Messaging Systems
- High-performance computing for real-time event detection, issue alarm and action taking.
- High-speed data communication to Control Center for real-time event alarm and action taking.
- Sufficient storage capacity for data and after managment.
- Supports multiple data input: Video Audio and Text.
Workstation-grade VMS for Real-time Rolling Stock Applications
With leading system performance, trusted mobile availability, flexible expansion functions, smart manageability, industrial-grade reliability, compact integrated features, Vecow fanless embedded workstation is your rugged & compact solution for performance-driven real-time VMS applications.
Key Features
- Workstation-grade 6-core Intel® Xeon®/Core™ processor and Intel® C246 chipset for real-time AI-oriented computing
- Fanless -40°C to 75°C operating temperature
- Powered Ethernet connections support max 12 cameras for video capture without additional power input
- Multiple WiFi/4G/3G/LTE/GPRS/UMTS connections support non-stop wireless communication
- 6V to 36V wide range DC power input with 80V surge protection
- Programmable ignition power control
- RAID 0, 1, 5, 10 data protection functions
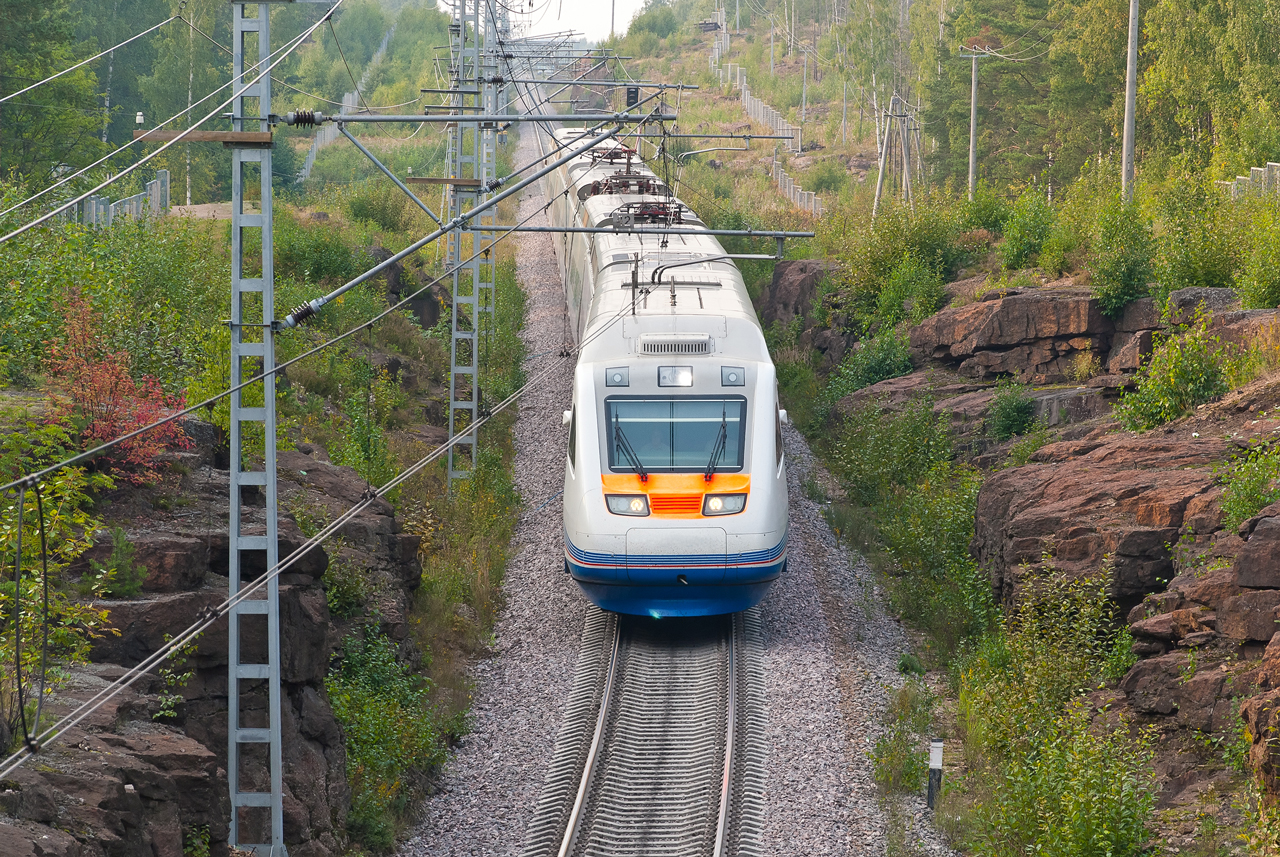
Pantograph Inspection System
3D Monitoring Secures Trusted Overhead Catenary System
Smart & Trusted Overhead Catenary System
The carbon brush on the pantograph has a groove at the bottom and is connected to the pantograph lift switch by air pressure. When the carbon brush is worn or broken, the pressure in the bottom groove will be reduced, and the linkage will be set immediately. The electric bow is lowered to ensure that the faulty carbon brush does not scratch the contact line, causing the tram line equipment to malfunction. In countries with cold climates, there is often an accident in which the carbon brushes are melted due to short-circuiting caused by snow trapping.
The installation method and quality of the carbon brush on the pantograph are closely related to the safety of the tram line, via the pantograph. The carbon brush is in smooth contact with the contact line to transmit power to the train. The contact line of the trolley line is erected by the left and right offset of the track center, so that the contact surface of the pantograph carbon brush and the contact line can be moved to the left and right on average to avoid wear of the carbon brush. The degree is not average. The collector bow carbon brush needs to be inspected regularly. Once it is found that abnormal wear or wear has reached the limit, it should be replaced immediately. The carbon brush may cause damage to the tram line equipment when the train is running at high speed. The bow and the tram line entangled the accident, the equipment loss is quite serious, so the preventive inspection of the pantograph carbon brush is very important.
Key Features of Pantograph Inspection System
- High-speed GigE PoE or USB data transfer for 3D camera data input.
- High-performance for 3D video data computing.
- High-speed WiFi/5G/4G/3G/LTE/GPRD/UMTS wireless data communication for event alarm.
- Remote data transfer for data backup and after management.
- Supports multiple data input : Video, Audio and Text.
Smart Pantograph AI Inspection System
Supporting high-resolution camera for image scanning, laser sensor for wire status detecting, AI-oriented machine learning given, web-based user-friendly management portal built-in, Vecow Smart Pantograph Inspection System not only gathers captured images and sensor data of the pantograph automatically but also identifies and alarms troubled issues to ensure a safe trip of each passing train.
Key Features
- Integrated pantograph monitoring solution.
- Reveal wear and damage to pantograph heads in real-time and on trains moving at full speed.
- Defective pantographs trigger automatic alarms day or night, around the clock.
- All maintenance tasks can be performed without any train traffic interruptions.
- Delivers benefits and value to infrastructure owners, rail operators and servicing companies.
- Passengers will enjoy improved railway traffic flow and increased scheduling stability.
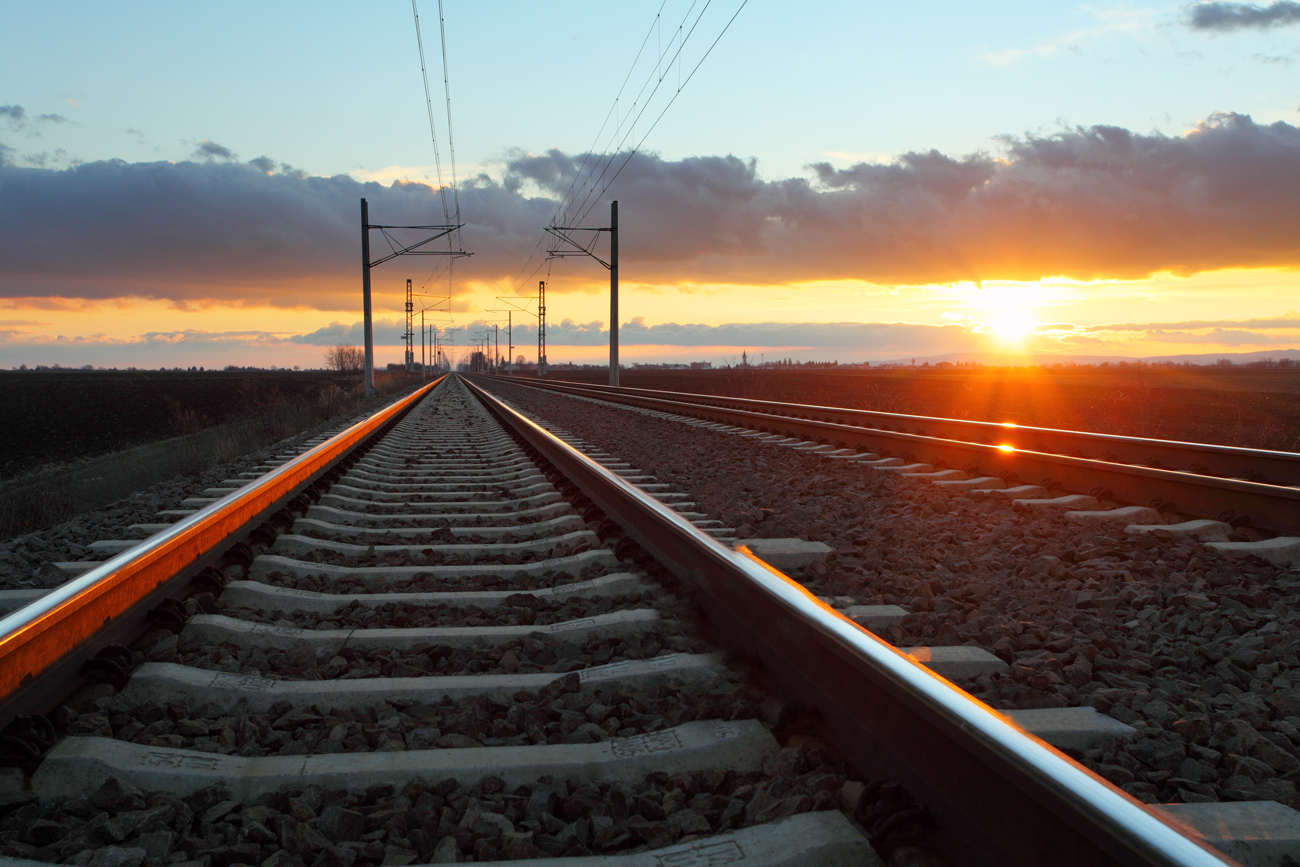
Railway Inspection System
Periodical AI Detecting Secures Rail Trail Infrastructure
Periodical Detection and Maintenance
The rails of the high-speed railway system are required to carry high-speed trains of more than 500 metric tons of trains for many years, which may cause internal damage to the rails that cannot be visually inspected. To ensure safety, the railway company introduces rail ultrasonic inspection vehicles, monitors the rails and repairs and repairs them to ensure that the rails are repaired and maintained. Operation and passenger safety.
Using sophisticated ultrasonic inspection technology to detect non-destructive detection on high-speed rails, it is possible to detect the metal fatigue caused by the train's high-speed driving after the high-speed driving, preventive maintenance, maintenance or arrange the rails. Replacement operations, with industrial lenses, use image recognition to enhance interpretation assistance and improve correctness. Not only will the safety of the high-speed rail and operation be greatly enhanced, but also the "early detection and pre-prevention" will ensure that no more serious rail breaks will occur.
Key Features of Railway Inspection System
- High-speed GigE PoE or USB data transfer for data input.
- High-performance for multiple data computing.
- GPS/WiFi/5G/4G/3G/LTE/GPRS/UMTS wireless data communication for event alarm.
- Remote data transfer for data backup and after management.
- Supports multiple data input : Video, Audio and Text.
Smart Railway AI Inspection System
Powered by workstation-grade processor, NVIDIA® graphics engine supporting up to 8K resolution and 7 independent HD displays, PCI/PCIe slot for multiple 10GigE LAN, PoE+, GigE LAN, LAN Bypass, or USB 3.0 expansions, smart power protection features, excellent mobile availability, industrial-grade reliability and all-in-one integrated functions, Vecow AI Computing System is your smart solution for Railway AI Inspection applications.
Key Features
- Workstation-grade Intel® platform running with NVIDIA® RTX/GeForce Series graphics for real-time AI computing
- Multiple GPS/WiFi/5G/4G/3G/LTE/GPRS/UMTS connections support non-stop wireless communication
- Max 10V to 36V wide range DC power input with 80V surge protection
- Programmable ignition power control
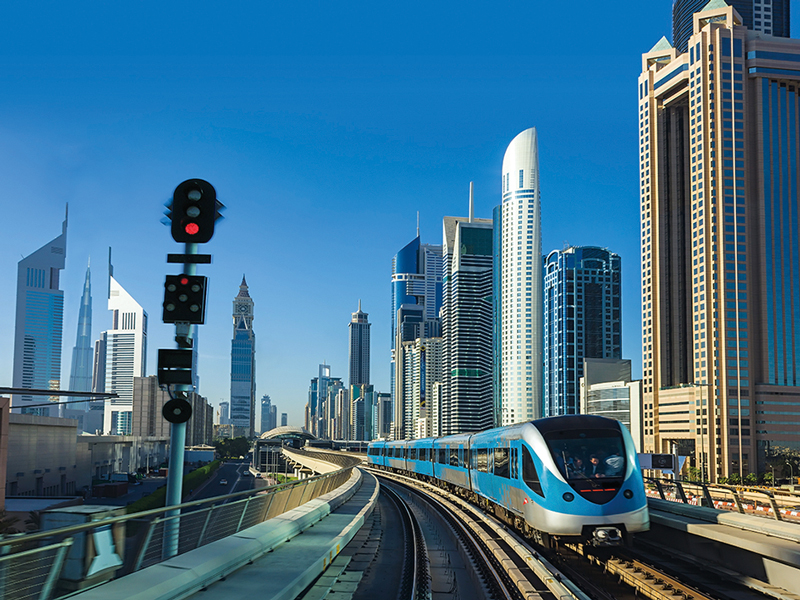
Visual Messaging System (VMS)
Wayside Sensor Integration Secures Rail Transport
VMS for Railroad Crossing System
Safety and reliability are necessary factors of a railway system. It matters large passenger capacity, high-speed transport and environment protection. Once an accident occurred, it will not only cause a major loss of life and property, but also bring a serious impact on the society. In addition, vehicles, people, animals, and accidents have caused casualties and property losses of up to millions of dollars, and once again caused people to pay attention to the safety of the road.
Visual Message System (VMS) is a smarter railway safety control solution in wayside. It integrates signal data, sensor data, video data, audio data, issue alarm, data computing, action taking, data backup and after analysis functions to secure rail transport anytime.
Key Features of Visual Messaging Systems
- High-performance computing for real-time event detection, issue alarm and action taking.
- High-speed data communication to Control Center for real-time event alarm and action taking.
- Sufficient storage capacity for data and after managment.
- Supports multiple data input: Video Audio and Text.
Workstation-grade VMS for Real-time Rolling Stock Applications
With leading system performance, trusted mobile availability, flexible expansion functions, smart manageability, industrial-grade reliability, compact integrated features, Vecow fanless embedded workstation is your rugged & compact solution for performance-driven real-time VMS applications.
Key Features
- Workstation-grade 6-core Intel® Xeon®/Core™ processor and Intel® C246 chipset for real-time AI-oriented computing
- Fanless -40°C to 75°C operating temperature
- Powered Ethernet connections support max 12 cameras for video capture without additional power input
- Multiple WiFi/4G/3G/LTE/GPRS/UMTS connections support non-stop wireless communication
- 6V to 36V wide range DC power input with 80V surge protection
- Programmable ignition power control
- RAID 0, 1, 5, 10 data protection functions
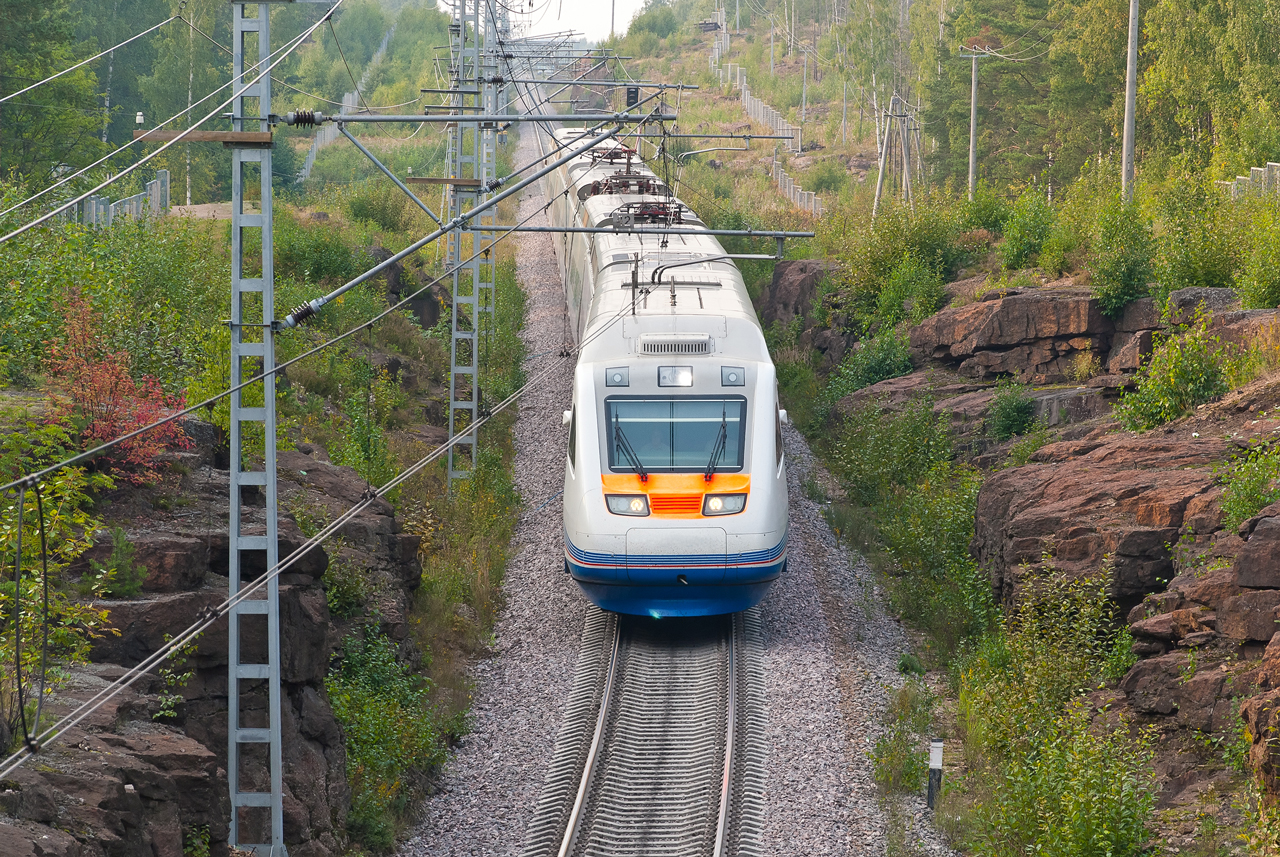
Pantograph Inspection System
3D Monitoring Secures Trusted Overhead Catenary System
Smart & Trusted Overhead Catenary System
The carbon brush on the pantograph has a groove at the bottom and is connected to the pantograph lift switch by air pressure. When the carbon brush is worn or broken, the pressure in the bottom groove will be reduced, and the linkage will be set immediately. The electric bow is lowered to ensure that the faulty carbon brush does not scratch the contact line, causing the tram line equipment to malfunction. In countries with cold climates, there is often an accident in which the carbon brushes are melted due to short-circuiting caused by snow trapping.
The installation method and quality of the carbon brush on the pantograph are closely related to the safety of the tram line, via the pantograph. The carbon brush is in smooth contact with the contact line to transmit power to the train. The contact line of the trolley line is erected by the left and right offset of the track center, so that the contact surface of the pantograph carbon brush and the contact line can be moved to the left and right on average to avoid wear of the carbon brush. The degree is not average. The collector bow carbon brush needs to be inspected regularly. Once it is found that abnormal wear or wear has reached the limit, it should be replaced immediately. The carbon brush may cause damage to the tram line equipment when the train is running at high speed. The bow and the tram line entangled the accident, the equipment loss is quite serious, so the preventive inspection of the pantograph carbon brush is very important.
Key Features of Pantograph Inspection System
- High-speed GigE PoE or USB data transfer for 3D camera data input.
- High-performance for 3D video data computing.
- High-speed WiFi/5G/4G/3G/LTE/GPRD/UMTS wireless data communication for event alarm.
- Remote data transfer for data backup and after management.
- Supports multiple data input : Video, Audio and Text.
Smart Pantograph AI Inspection System
Supporting high-resolution camera for image scanning, laser sensor for wire status detecting, AI-oriented machine learning given, web-based user-friendly management portal built-in, Vecow Smart Pantograph Inspection System not only gathers captured images and sensor data of the pantograph automatically but also identifies and alarms troubled issues to ensure a safe trip of each passing train.
Key Features
- Integrated pantograph monitoring solution.
- Reveal wear and damage to pantograph heads in real-time and on trains moving at full speed.
- Defective pantographs trigger automatic alarms day or night, around the clock.
- All maintenance tasks can be performed without any train traffic interruptions.
- Delivers benefits and value to infrastructure owners, rail operators and servicing companies.
- Passengers will enjoy improved railway traffic flow and increased scheduling stability.
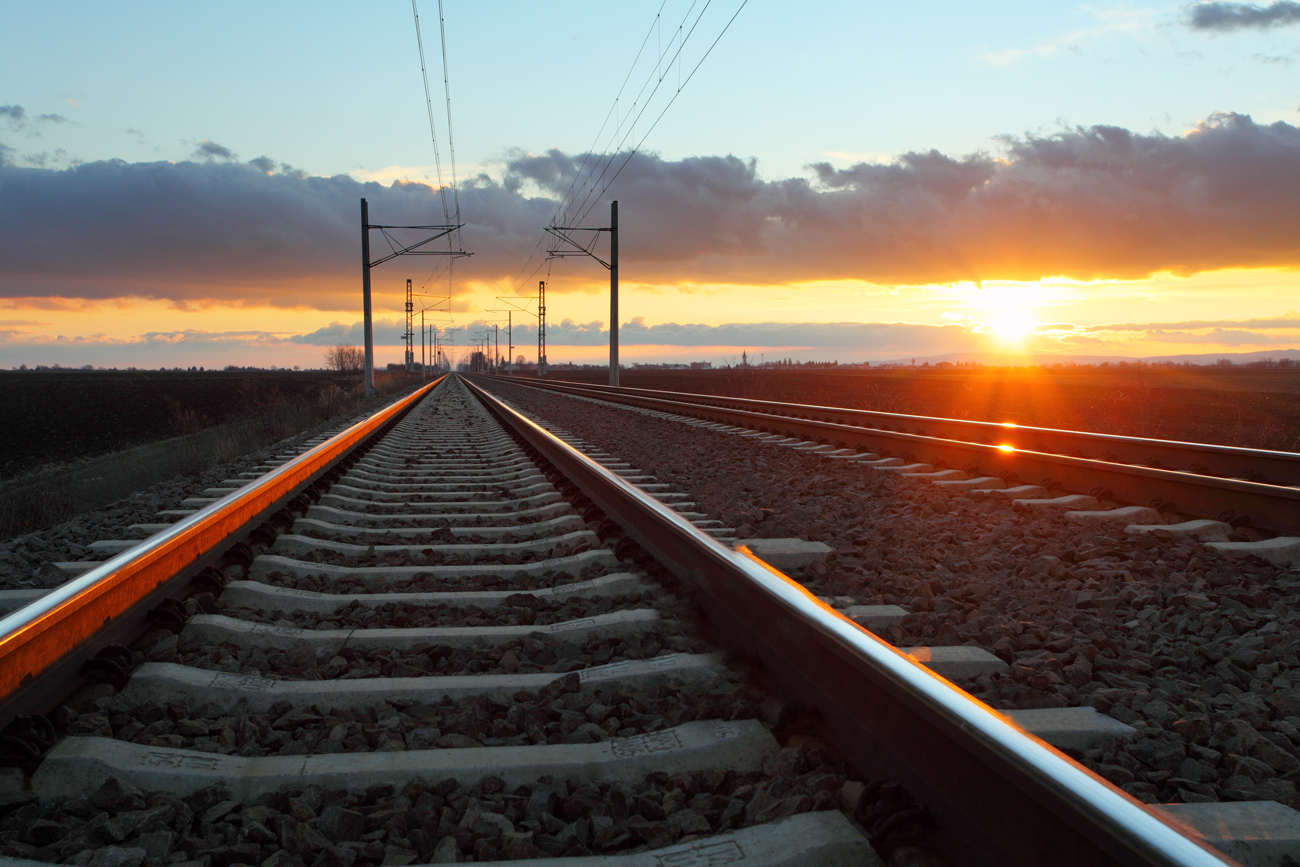
Railway Inspection System
Periodical AI Detecting Secures Rail Trail Infrastructure
Periodical Detection and Maintenance
The rails of the high-speed railway system are required to carry high-speed trains of more than 500 metric tons of trains for many years, which may cause internal damage to the rails that cannot be visually inspected. To ensure safety, the railway company introduces rail ultrasonic inspection vehicles, monitors the rails and repairs and repairs them to ensure that the rails are repaired and maintained. Operation and passenger safety.
Using sophisticated ultrasonic inspection technology to detect non-destructive detection on high-speed rails, it is possible to detect the metal fatigue caused by the train's high-speed driving after the high-speed driving, preventive maintenance, maintenance or arrange the rails. Replacement operations, with industrial lenses, use image recognition to enhance interpretation assistance and improve correctness. Not only will the safety of the high-speed rail and operation be greatly enhanced, but also the "early detection and pre-prevention" will ensure that no more serious rail breaks will occur.
Key Features of Railway Inspection System
- High-speed GigE PoE or USB data transfer for data input.
- High-performance for multiple data computing.
- GPS/WiFi/5G/4G/3G/LTE/GPRS/UMTS wireless data communication for event alarm.
- Remote data transfer for data backup and after management.
- Supports multiple data input : Video, Audio and Text.
Smart Railway AI Inspection System
Powered by workstation-grade processor, NVIDIA® graphics engine supporting up to 8K resolution and 7 independent HD displays, PCI/PCIe slot for multiple 10GigE LAN, PoE+, GigE LAN, LAN Bypass, or USB 3.0 expansions, smart power protection features, excellent mobile availability, industrial-grade reliability and all-in-one integrated functions, Vecow AI Computing System is your smart solution for Railway AI Inspection applications.
Key Features
- Workstation-grade Intel® platform running with NVIDIA® RTX/GeForce Series graphics for real-time AI computing
- Multiple GPS/WiFi/5G/4G/3G/LTE/GPRS/UMTS connections support non-stop wireless communication
- Max 10V to 36V wide range DC power input with 80V surge protection
- Programmable ignition power control