Freight
Researchers opt for Blickfeld’s LiDAR technology to enhance rail freight
Pyramid schemes: a look into Egypt’s megaprojects
A SAMIRA research project looking into shunting assistance systems for freight has turned to Blickfeld to use the firm’s LiDAR technology in the project. Jasleen Mann reports.
L
iDAR sensor technology company Blickfeld is providing sensor solutions to FH Aachen for research and developments in railway automation. The research is EU-funded and expects to develop a train shunting assistance system and improve the automated detection of objects on tracks.
FH Aachen is a part of the consortium working on the project, dubbed SAMIRA (Shunting Assistant and Monitoring Interface for Autonomous Rail Applications), in which the train shunting assistance system will be based on an advanced sensor set which will include the LiDAR technology.
In addition, accuracy relating to the automated detection of objects on the tracks will assist in avoiding collisions and increase worker safety.
Brightline senior vice president, corporate affairs, Ben Porritt
Shunting solutions
Florian Petit, co-founder and CEO at Blickfeld, says: “Although today’s technologies are ever advancing, the rail industry is still coming face to face with safety issues and inefficiencies that affect the transportation of goods and people.
“More specifically, the process of shunting freight trains has been proven to be extremely dangerous and time-consuming, particularly when doing so in hazardous weather conditions. The driver has to frequently walk along the train for direction shifts, or an assistant has to stand on the last wagon’s platform reporting any obstacles that might affect the train’s pathway via radio.”
Hiring personnel to report these obstacles is difficult because of the level of expertise and caution required. The first and last miles of a freight wagon’s journey are costly and labour intensive, with minor accidents occurring more frequently than on mainline railways.
The LiDAR sensors are installed at the back of the train, allowing the driver to see behind the train and detect objects on the track. The assistance system integrates Blickfeld’s solid-state 3D LiDAR sensors, with a 70 degree field of view, and long-distance detection of up to 150 metres, enabling track monitoring to take place where the track is curved.
As the sensors are software-based, they can be customised to any field of view and solution without complex modifications. The track area when a train is reversing can be monitored by a stereo camera for close-range detection, two additional cameras that provide data basis for algorithm-based object detection, and a radar sensor.
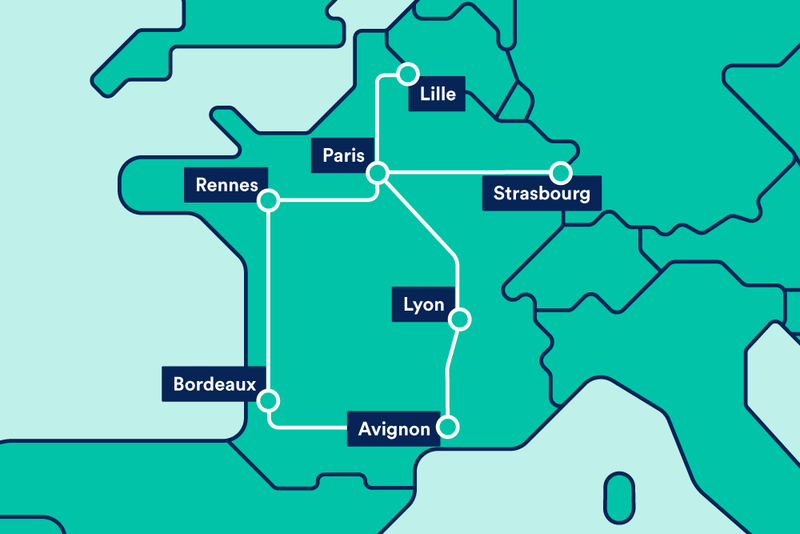
Map of french high speed network
The best way of getting passengers off planes and onto trains is simple. Remove the choice.
Applications outside of rail freight
Using camera images and 3D point clouds detection of objects is made possible alongside mutual control of the different sensors. Train drivers can view the information through a live feed on a tablet that indicates hazards.
“LiDAR sensors’ ability to measure distances is particularly valuable, compared to a camera’s function of merely perceiving colours. This is a fundamental difference that plays a key role in mobility solutions,” says Petit
“After all, distance is the decisive factor when avoiding collisions, which must be measured quickly, reliably, and accurately. In addition to the immediate benefits, such as operational efficiency and personnel safety, the introduction of autonomous functions also has broader implications, like promoting the smooth operation of train traffic overall.”
In order to find the trajectory of the vehicle, Blickfeld is working on visual and sensors and maps as the tight structure gauge is the main challenge. The space that the vehicle has to move needs to be ensured.
“The research conducted to date proves to be incredibly beneficial for the operation of freight trains, inevitably developing a safe, autonomous shunting assistance system that can be implemented throughout train stations across the globe,” Petit ecplains.
“More generally, we believe LiDAR’s potential within the industry is endless – whether it’s for measuring a freight train’s volume on the tracks, counting people on the platforms, or providing reliable and instant data to staff on the ground, the technology’s vast capabilities make Lidar applicable in many areas.”
Main image: A BNSF Railway freight train snakes along the Clark Fork River near Thompson Falls, MT. Credit: Drew Halverson | Shutterstock